Introduction
When you maintain your ice machine, you are not only ensuring that you will have ice available when you require it, but you are also ensuring that your appliance will last as long as possible and function well. It is important to perform routine maintenance on your machine to guarantee that it functions without any hiccups and to prevent common problems that could cause it to function without creating ice. This book will not only lead you through the “how” of maintaining your ice machine, but it will also walk you through the “when” and “why” of doing so, so minimizing annoying downtimes and making repairs that are expensive. https://amzn.to/3WoePQf
Understanding Your Ice Machine
Understanding the basic operation and mechanics of your ice machine is crucial for diagnosing and fixing issues such as when the ice machine is running but not making ice. Here’s what you need to know:
- Basic Mechanics: At its core, an ice machine works by freezing water directly from a water supply line, usually involving a freezing tray or an evaporator. A refrigerant system cools down the water until it turns into ice.
- Operation Cycle: The typical cycle starts with water filling the ice mold, followed by the cooling phase where the refrigerant lowers the temperature significantly. Once the ice is formed, the machine shifts to harvest mode, where the ice is heated slightly to detach it from the tray and collected in the bin.
- Key Components: Understanding the components can help in troubleshooting. Major components include:
- Water inlet valve: Allows water to enter and is crucial in the ice-making process.
- Evaporator: Where the actual freezing of the water takes place.
- Thermostat: Monitors the temperature to start the harvest cycle at the right moment.
- Heater: Loosens the ice from the evaporator.
- Ice mold: Shapes the ice.
- Common Types of Ice Machines:
- Modular Ice Machines: These are common in commercial settings, producing large amounts of ice.
- Undercounter Ice Machines: Compact and ideal for small spaces like bars or small restaurants.
- Countertop Ice Dispensers: Often seen in healthcare settings, these produce nugget-style ice and dispense water as well.
- Maintenance Needs by Type: Each type of ice machine has its specific maintenance requirements which can affect their performance and longevity.
- Modular units require frequent cleaning of their air filters and regular descaling.
- Undercounter units need their water filters changed regularly and the ice bin cleaned to prevent mold.
- Countertop dispensers need constant cleaning to maintain hygiene due to their direct contact with drinking water.
By familiarizing yourself with these aspects, you can better identify why your ice machine is running but not making ice, and apply the appropriate fixes to ensure it runs efficiently.

Common Reasons Why Ice Machines Stop Making Ice
When your ice machine is running but not making ice, it can be both perplexing and frustrating. Understanding the common causes behind this issue is key to resolving it swiftly. Below are several factors that could be affecting your machine’s ability to produce ice:
- Water Supply Issues
- Insufficient water flow: A significant decrease in water flow can prevent ice formation.
- Blocked water filters: Over time, filters can become clogged with sediment and minerals, restricting water flow.
- Faulty water inlet valve: If this valve is damaged, it may not open sufficiently to allow water into the ice mold.
- Temperature Problems
- Incorrect freezer temperature: The freezer section must reach a certain temperature to initiate the ice-making process.
- Frequent door openings: Excessive opening of the machine door can raise the temperature, affecting ice production.
- Mechanical Failures
- Worn out pump: Essential for circulating water in the machine, a malfunctioning pump can halt ice production.
- Thermostat issues: A faulty thermostat may fail to trigger the ice-making cycle due to incorrect temperature readings.
- Electrical Problems
- Sensor malfunctions: Sensors that determine when to start and stop ice production can malfunction, leading to a halt in ice output.
- Control board issues: A defective control board can disrupt the operational sequences necessary for ice production.
Identifying the root cause from these common issues is the first step in getting your ice machine back to its optimal working condition. Each problem listed can significantly impact the function of your machine, highlighting the importance of regular maintenance and timely repairs. https://amzn.to/3WoePQf
Preventative Maintenance Schedule
Maintaining your ice machine efficiently requires a regular schedule to avoid common issues like ice machine running but not making ice. A consistent maintenance routine not only keeps your machine in optimal condition but also significantly reduces the likelihood of mechanical failures. Here’s a detailed maintenance schedule that you should follow:
- Daily Maintenance Tasks:
- Inspect and clean the exterior surfaces to prevent dust and grime accumulation which can affect the overall thermal efficiency of the machine.
- Check the water filter and replace it if necessary to ensure a clean water supply, which is crucial for making clear ice.
- Weekly Maintenance Tasks:
- Sanitize the interior surfaces and ice storage bin to prevent the buildup of bacteria and mold that could contaminate the ice.
- Verify that the water lines are clear of any obstructions and that the flow is consistent, addressing any anomalies immediately.
- Monthly Maintenance Tasks:
- Deep clean the entire machine using approved cleaners to remove any scale buildup in the water system, which can hinder ice production.
- Inspect the condenser coil and clean it to ensure it is free from dust and lint, which can reduce the machine’s ability to cool efficiently.
- Yearly Maintenance Tasks:
- Schedule a professional inspection of the refrigeration system to ensure all components are functioning correctly.
- Check and recalibrate the thermostat and other controls to ensure the settings are optimal for ice production.
If you adhere to this preventative maintenance program, you can significantly reduce the likelihood that your ice maker will operate but will not produce ice under the circumstances. It is important to perform routine maintenance on the machine since it not only improves its efficiency but also extends its lifespan. This ensures that you can depend on it to create ice whenever it is required.
Keep in mind that preventative maintenance is essential. It is much simpler to avoid problems than it is to get them fixed once they have already made your operations more difficult. When carrying out any maintenance duties, it is imperative that you always keep in mind the particular model of your machine as well as the operational rules.
Step-by-Step Maintenance Guide
When your countertop ice maker won’t make ice, it could be due to several issues, often related to maintenance oversights. Here’s a comprehensive guide to help you diagnose and fix common problems, ensuring your ice maker operates efficiently:
- Inspect and Clean the Water Filter
- Over time, the water filter in your ice maker can become clogged with impurities and scale, reducing water flow to the ice-making unit, which can prevent ice production.
- Monthly Check: Inspect the filter for debris and clean it according to the manufacturer’s instructions. If it’s beyond cleaning, replace it to restore proper water flow.
- Check Water Supply Lines
- Inadequate water supply can be a primary reason your ice maker isn’t producing ice. Ensure there are no kinks or leaks in the water supply line.
- Bi-Annual Inspection: Examine hoses for signs of wear or damage. Replace if necessary to prevent disruptions in water supply.
- Clean and Sanitize Ice Making Components
- Residue and mineral build-up in the ice tray or on the evaporator can hinder the ice-making process.
- Quarterly Cleaning: Use a nickel-safe cleaner to scrub the ice tray and evaporator. Rinse thoroughly with water to prevent flavor transfer.
- Inspect and Adjust the Freezer Temperature
- If the freezer section of your ice maker is too warm, ice won’t form efficiently.
- Regular Monitoring: Check the temperature settings. It should be set between 0°F and 5°F. Adjust if necessary.
- Examine the Condenser Coils
- Dirty condenser coils can impair the cooling ability of your ice maker, affecting ice production.
- Bi-Annual Cleaning: Use a coil brush and vacuum to remove dust and lint from the condenser coils. Ensure adequate airflow around the coils.
- Check the Ice Machine’s Sensor
- Sensors in ice makers ensure proper ice cube size and prevent overfilling. A malfunctioning sensor can stop ice production.
- Annual Check: Clean the sensor with a soft cloth. If problems persist, consult the manufacturer’s guide or contact a technician for potential replacement.
- System Reset
- Sometimes, simply resetting your ice maker can resolve minor glitches and restore normal function.
- As Needed: Unplug the ice maker for a few minutes, then plug it back in. This can help reset the system’s internal processor and clear errors.
- Review the User Manual for Specific Troubleshooting
- Each model may have unique features and troubleshooting steps.
- Ongoing Reference: Keep your user manual accessible for specific troubleshooting instructions tailored to your ice maker model.
Maintaining your countertop ice maker on a regular basis is essential if you want it to function at its best and last as long as possible. If you follow these instructions, you will be able to ensure that your machine continues to create ice of a good quality while also avoiding the typical problem of the countertop ice maker not producing ice. Always keep in mind that if you are unsure of the problem or if it continues, it is best to get in touch with a professional expert in order to avoid causing any further harm to your appliance.
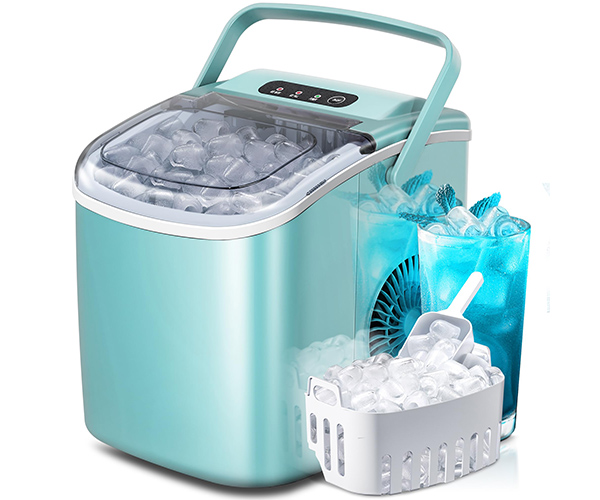
When to Call a Professional
Maintaining a countertop ice maker isn’t always straightforward, especially when troubleshooting complex issues. Recognizing when professional help is needed can save you time and prevent further damage to your machine. Here are some signs that it might be time to call in the experts, particularly if your countertop ice maker won’t make ice:
- Persistent Operational Issues: If your troubleshooting attempts haven’t resolved the ice-making issue, it’s a clear signal for professional assessment.
- The machine operates but fails to produce ice.
- Strange noises or vibrations during operation.
- Electrical Problems: Any electrical faults, such as failure to power on or frequent power interruptions, should be handled by a professional to ensure safety and functionality.
- Unusual electrical smells or sparks.
- Breaker trips when the ice maker is turned on.
- Water Leakage: Water around the machine isn’t just a nuisance; it can also be a hazard and a sign of internal issues.
- Constant water pooling under or around the machine.
- Signs of water damage to surrounding areas.
- Ice Quality Concerns: If the ice produced is of poor quality, it might indicate deeper issues with the filtration system or internal mechanics.
- Ice cubes are smaller than usual or are not forming properly.
- Ice tastes bad or has an unusual smell.
- Repeated Freeze-ups: Frequent freeze-ups within the machine, despite routine maintenance, often require the skills of a technician.
- Ice formation around the evaporator.
- Blockages in the water lines despite regular cleaning.
In any of these scenarios, contacting a certified technician who specializes in ice machine maintenance is crucial. They can provide a thorough diagnosis and the appropriate repairs, ensuring that your machine returns to optimal working condition. Professional help not only fixes the issue at hand but also helps in extending the lifespan of your ice maker, ultimately saving you money and inconvenience in the long run.
It’s essential to choose a reputable and experienced service provider. Ensure that they:
- Have positive reviews and testimonials.
- Offer a warranty on their work.
- Provide clear and upfront pricing.
By staying vigilant and recognizing the signs that require professional intervention, you can maintain the performance and longevity of your countertop ice maker. Always remember, the cost of a professional fix can often outweigh the expense of a complete machine replacement due to DIY repair attempts going wrong. https://amzn.to/3WoePQf
Extending the Life of Your Ice Machine
Proper maintenance not only fixes issues like when your countertop ice maker won’t make ice, but it also extends the life of your ice machine significantly. Below are key practices that can help you maximize the longevity and efficiency of your ice machine:
- Regular Cleaning and Descaling:
- Remove mineral deposits that can build up in your machine, especially if you have hard water. These deposits can clog your machine and affect ice production.
- Use a manufacturer-approved descaling agent to clean your ice machine at least twice a year.
- Routine Inspections:
- Check for signs of wear and leaks periodically. Hoses and fittings can become loose over time, leading to water inefficiencies or damage to internal components.
- Ensure that the environment around your ice machine supports its efficiency, such as keeping it at the recommended operating temperatures.
- Filter Replacements:
- Regularly replace water filters according to the manufacturer’s guidelines. Clean filters help prevent impurities and scale buildup, which are common reasons a countertop ice maker won’t make ice.
- Maintaining clean filters not only ensures better quality ice but also reduces strain on the machine’s components.
- Proper Usage and Handling:
- Avoid overloading the machine beyond its capacity. Consistent overloading can lead to premature wear and tear.
- Train all users on the correct operation procedures to avoid mishandling, which can lead to mechanical failures.
- Timely Repairs:
- Address any issues as soon as they appear, even if they seem minor. Early detection and repair can prevent more significant problems down the line, especially in cases where your countertop ice maker won’t make ice.
- Upgrade Parts When Necessary:
- As your ice machine ages, certain components may need to be upgraded or replaced. Keep an eye on the efficiency of parts like thermostats and motors, and consult with a professional about timely upgrades.
It is possible that if you follow these suggestions, your ice machine will not only continue to function effectively, but it will continue to do so for a longer period of time, which will reduce the total frequency of repairs as well as the related costs. Keep in mind that the key to lifespan is not simply doing routine maintenance on your ice machine, but also having a grasp of its specific requirements and the limits of its operation.
Conclusion
Regular maintenance of your ice machine is not just a routine chore; it’s a crucial practice that ensures the efficient and prolonged use of your equipment. By understanding and implementing the advice shared in this guide, you can:
- Prevent common issues like countertop ice maker not freezing.
- Extend the operational lifespan of your machine, making it a reliable part of your daily life or business.
Here are key takeaways to ensure your ice machine remains in peak condition:
- Regular Checks: Periodically inspect your machine for any signs of wear or operational issues.
- Timely Maintenance: Don’t wait for a complete failure. Addressing issues early can prevent more serious problems.
- Professional Assistance: When in doubt, consult with a professional technician to handle complex issues.
By staying proactive about maintenance, you can avoid the inconvenience and expense of a non-functional ice machine. Remember, a little attention goes a long way in maintaining the health of your appliance. Keep these practices in mind, and your ice maker should serve you well for years to come.
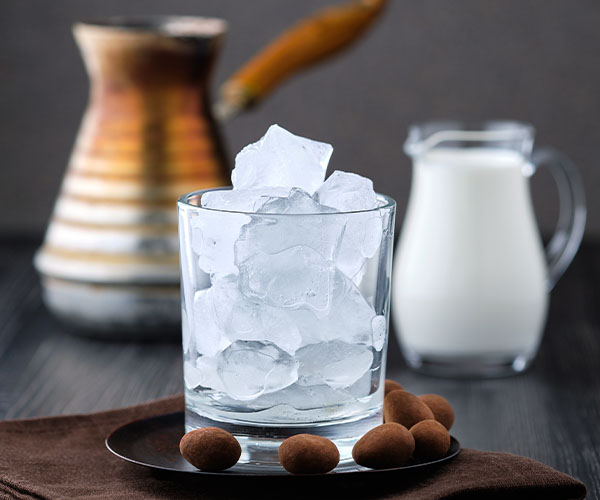
Frequently Asked Questions about Maintaining Your Ice Machine
1. How often should I clean my ice machine?
Answer: Clean your ice machine at least once every six months to ensure it operates efficiently and maintains ice quality.
2. What signs indicate that my ice machine needs maintenance?
Answer: Look for signs like smaller ice cubes, longer freeze times, unusual noises, or any error messages on the display panel.
3. Can I perform maintenance on my ice machine myself?
Answer: Yes, basic maintenance like cleaning and replacing filters can be done by yourself. However, for more technical issues, it’s advisable to call a professional.
4. What materials do I need to clean my ice machine?
Answer: You will need ice machine cleaner (specific to your model), a soft rag, a nylon brush, and protective gloves.
5. How do I know if my ice machine needs a filter change?
Answer: Check the manufacturer’s guidelines; generally, filters should be changed every 3 to 6 months, depending on usage.
6. What are the consequences of not maintaining my ice machine?
Answer: Neglecting maintenance can lead to inefficiencies, increased energy costs, shorter lifespan of the machine, and poor quality of ice.
7. How does hard water affect my ice machine?
Answer: Hard water can lead to scale buildup inside the machine, which can obstruct water flow and reduce efficiency. Using a water softener or frequently descaling the machine can help.
8. Is there a best season to perform maintenance on my ice machine?
Answer: Maintenance can be performed any time of year, but it’s a good idea to service your machine before peak usage seasons, like summer, to ensure it operates flawlessly when you need it most.