Introduction: Setting the Stage
Even though every appliance has its own peculiarities, the fact that your ice maker suddenly stops producing ice is more than just a little inconvenience; it has the potential to completely interrupt your routine. Being someone who has experienced this icy difficulty firsthand during a family gathering, I can empathize with the frustration that it causes. Does the issue consist of something as straightforward as a mechanical glitch, or is there something more complicated at play here? This article takes a deep dive into the inner workings of ice machines to determine whether or not electrical problems are the cause of the chilling silence that your machine is producing. I invite you to accompany me as we investigate the complex mechanisms that these cool buddies use to ensure that your ice is available when you require it the most. https://amzn.to/3WoePQf
Understanding Your Ice Machine
To effectively troubleshoot why your ice machine is running but not making ice, it’s essential to start with a solid understanding of how these devices operate. Here’s a breakdown of their mechanisms and components:
- Basic Working Principle: At its core, an ice machine freezes water from a supply line into sheets or cubes, which are then broken down into usable ice. The process involves an evaporator, a compressor, and a condenser.
- Key Components:
- Evaporator: Where the water freezes, forming ice.
- Compressor: Drives the refrigerant through the system, essential for the cooling process.
- Condenser: Releases accumulated heat from the machine outside.
- Water Inlet Valve: Controls water flow into the machine; issues here can prevent ice formation.
- Thermostat: Regulates the temperatures, ensuring optimal ice production conditions.
- Importance of Maintenance:
- Regular Cleaning: Residual minerals from water can build up, affecting the efficiency and functionality of the ice machine.
- Routine Inspections: Regular checks can help catch issues like worn out seals or electrical faults before they lead to more significant problems.
- Professional Servicing: Ensures that more complex components, like the compressor and evaporator, are in good working order.
When trying to determine why an ice machine is operating but not producing ice, it is essential to have a thorough understanding of these aspects. Because every component plays a crucial part, even a single fault in any one of them might cause the entire process to be disrupted. As long as you do routine maintenance on your ice machine, you can not only extend its lifespan but also ensure that it functions well, allowing you to continue to receive ice cubes at the precise moment that you require them.
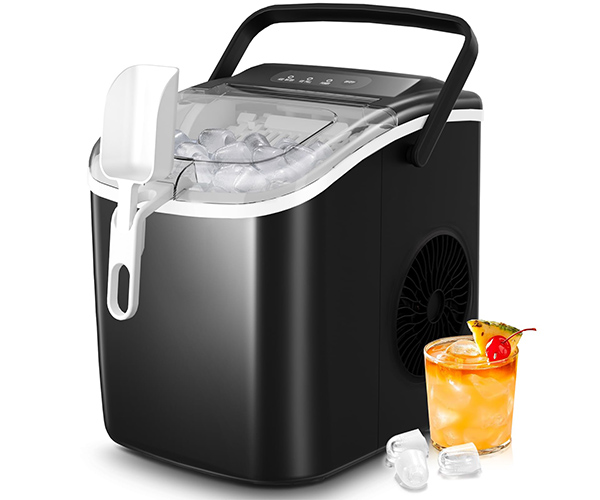
Symptoms of Electrical Problems in Ice Machines
When your ice machine is running but not making ice, pinpointing electrical issues can be a complex endeavor. Here’s what you need to watch for:
- Unexpected Stops and Starts: If your ice machine frequently halts its cycle or restarts unexpectedly, it could indicate electrical instability. Such symptoms often suggest issues with the machine’s electronic control board or wiring faults.
- Unusual Noises: Electrical components in distress often emit unusual noises. Buzzing or humming sounds can signal that electrical currents are not flowing properly through the machine.
- Failure to Start: A clear sign of an electrical issue is when your ice machine fails to start despite being plugged in and turned on. This could be due to faulty electrical connections or a defective motor.
- Inconsistent Ice Production: If the ice machine begins the ice-making process but fails to produce ice, or the ice production is erratic, this might be related to electrical sensors or heating elements malfunctioning.
- Electrical Smells or Signs of Burning: Any smell of burning or visible signs of scorched wires are urgent symptoms of electrical problems. These should be addressed immediately to prevent potential safety hazards.
- Display Errors: Many modern ice machines have digital displays that provide error codes or alerts when there’s an electrical issue. Familiarize yourself with these codes, as they can offer direct clues about what might be wrong.
These symptoms, if observed, should prompt further investigation or professional assessment to ensure that the ice machine running but not making ice issue is resolved safely and effectively. Remember, handling electrical components can be dangerous; it is often best to consult with or hire a professional technician who can diagnose and fix the issue without risking further damage or personal injury.
Troubleshooting Electrical Issues
When your ice machine is running but not making ice, it could signal a deeper electrical issue. To ensure you tackle this problem effectively, follow this step-by-step guide to troubleshooting the electrical components of your ice machine:
- Check the Power Supply
- Ensure that your ice machine is plugged into a working outlet. Sometimes, the simplest issues like loose plugs or tripped circuit breakers can be the culprit.
- Verify that the voltage at the outlet matches the specifications of your ice machine. An incorrect voltage can prevent the machine from operating properly.
- Inspect the Control Module
- The control module is the brain of your ice machine. Check for any error codes that might indicate what the issue could be. Consult your machine’s manual for guidance on what each code means and the recommended actions.
- Reset the control module by turning off the power to the machine for a few minutes. This can sometimes clear transient errors that cause the machine to malfunction.
- Examine the Water Supply and Fill Valve
- A common issue for an ice machine running but not making ice is a malfunctioning fill valve. Ensure that the valve is functioning properly and that water flows freely into the machine.
- Check for any kinks or blockages in the water line that might restrict flow to the machine. A sufficient water supply is crucial for ice production.
- Assess the Evaporator and Ice Making Assembly
- Ice machines rely on the evaporator to freeze the water into ice. Look for signs of frost or ice buildup around the evaporator, which can indicate temperature regulation issues.
- Ensure that the ice-making assembly is not obstructed. An obstruction can prevent the machine from cycling through its ice-making process.
- Monitor the Condenser and Fan
- The condenser unit plays a critical role in dissipating heat. If the condenser coils are dirty or the fan is malfunctioning, it can lead to poor cooling performance.
- Clean the condenser coils regularly and verify that the fan operates at the correct speed and without abnormal noise.
- Safety First
- When dealing with electrical components, always ensure the power is disconnected before starting any inspections to avoid the risk of shock.
- Consider wearing protective gear, such as gloves and goggles, to protect yourself during the troubleshooting process.
If after all these steps your ice machine still fails to produce ice, it might be time to call a professional technician. They can provide a more thorough diagnosis and ensure that any complex electrical issues are resolved safely and effectively.
By systematically addressing each potential electrical issue, you can better understand why your ice machine is running but not making ice and take appropriate action to fix the problem.
Preventive Measures and Regular Maintenance
Regular maintenance is not just about ensuring your countertop ice maker keeps running; it’s about preventing those days when your countertop ice maker won’t make ice. Here’s a detailed guide on how to maintain your ice maker to ensure optimal performance:
- Regular Cleaning:
- Ice makers should be cleaned at least once every six months. This involves turning off the machine, removing any ice, and cleaning all surfaces with a mild detergent.
- Pay special attention to removing scale and mineral deposits, which can build up and impede ice production.
- Inspect and Replace Water Filters:
- If your ice maker has a water filtration system, check and replace the filters according to the manufacturer’s guidelines. Dirty filters can restrict water flow and affect ice quality.
- Check and Tighten Electrical Connections:
- Loose electrical connections can lead to operational failures. Periodically checking and tightening these connections can prevent electrical issues that might stop the machine from making ice.
- Verify Freezer Temperature Settings:
- Ensure that the freezer temperature is set to an optimal level that supports ice production. Too high or too low temperatures can prevent ice from forming.
- Annual Service Check-Up:
- Have a professional technician inspect your ice maker annually. They can diagnose and fix issues that might not be evident to untrained eyes.
- Be Proactive with Replacement Parts:
- Keep an eye on the lifespan of critical components like the ice mold and the heating element. Replacing them before they fail can prevent periods when your machine can’t produce ice.
- Monitor for Unusual Noises or Cycles:
- Unusual noises or extended cycles can be early indicators of a problem. Addressing these early can prevent more significant issues down the line.
By following these steps, you can greatly reduce the chances of your countertop ice maker failing to produce ice. Regular maintenance not only extends the life of your appliance but also ensures it runs efficiently, saving you time and inconvenience in the long run.
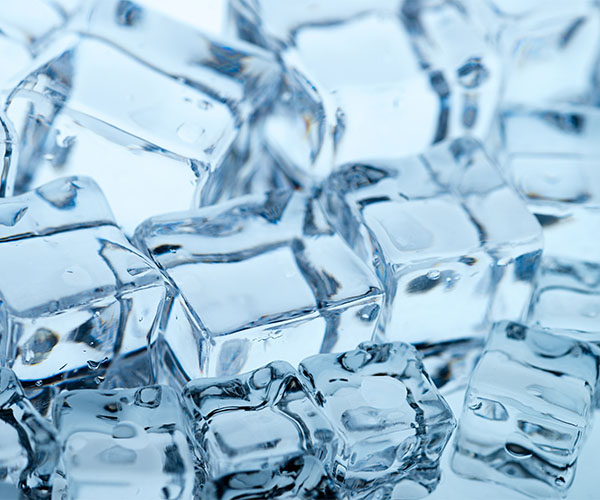
Expert Insights
Over the course of our investigation into the enigma of why your countertop ice maker is unable to produce ice, we have conferred with a number of professionals in the field. Especially when it comes to electrical problems that might not be immediately obvious, their insights are essential in order to successfully navigate the often complicated world of appliance repair. This is what they had to say about it: https://amzn.to/3WoePQf
- Understanding the Basics: It’s essential to grasp that most problems related to countertop ice makers not making ice stem from electrical discrepancies. Experts emphasize that an understanding of your machine’s electrical system is key.
- Circuit Check: Regularly inspect the ice maker’s circuitry for any signs of damage or wear. An unnoticed issue here can lead to bigger problems.
- Power Supply Consistency: Ensure that your ice maker is receiving a consistent power supply, which is crucial for optimal performance.
- Advanced Troubleshooting Techniques:
- Voltage Testing: Using a multimeter to check the voltage at various points of the ice maker can help isolate electrical faults.
- Component Testing: Specific electrical components, such as the solenoid or thermostat, can fail and cause the machine to stop producing ice.
- Insights from the Field: Technicians often share anecdotes about seemingly minor issues that led to major repairs. One common theme is the underestimation of routine maintenance and how it can prevent most electrical issues.
- Example Case: A professional recalled a case where a simple reset of the ice maker’s internal circuit breaker resolved an issue that had been misdiagnosed as a costly compressor failure.
- Expert Recommendations:
- Regular Inspections: Schedule regular inspections with a certified technician to ensure all components are functioning correctly.
- Educate Yourself: Understanding basic electrical concepts can help you troubleshoot issues before they require professional intervention.
- Preventative Maintenance: Don’t wait for a breakdown. Proactively replacing worn-out parts can save time and money in the long run.
In conclusion, while it may be tempting to immediately assume that your ice maker’s problems are complex, often the solution lies in addressing simple electrical issues that can be easily overlooked. By following these expert recommendations and maintaining a keen eye on the health of your appliance’s electrical system, you can ensure its longevity and performance.
Remember, a well-maintained ice maker is less likely to give you trouble when you least expect it.
Alternative Causes of Problems
While electrical faults often take the blame when your countertop ice maker won’t make ice, there are other non-electrical issues that could be disrupting your machine’s performance. Understanding these can save you time and unnecessary repairs. Here’s what you should consider:
- Mechanical Failures:
- Ice Maker Motor: If the motor that drives the ice ejector arms is faulty, no ice will be produced.
- Water Inlet Valve: A malfunction here can prevent water from entering the ice-making mechanism, crucial for ice formation.
- Water Flow Issues:
- Clogged Filter: A dirty filter can restrict water flow to the ice maker, impacting ice production.
- Low Water Pressure: Ice makers require a minimum water pressure to function correctly; too low, and ice won’t form.
- Sensor Problems:
- Thermostat Malfunctions: If the ice maker’s thermostat is inaccurate, it may not trigger the ice production cycle.
- Bin Sensor Issues: Overfilled ice bins can trigger sensors that halt production; make sure the bin isn’t blocked.
- Environmental Factors:
- Ambient Temperature: Too high or too low room temperatures can affect the machine’s efficiency.
- Ventilation: Poor ventilation around your ice machine can lead to overheating, especially in compact spaces.
- Maintenance Lapses:
- Regular Cleaning: Lack of regular cleaning can lead to build-ups that interfere with various mechanical components.
- Seasonal Servicing: Not servicing your ice machine as recommended can lead to accumulated issues that manifest as non-functionality.
Understanding these potential problems helps in diagnosing why your countertop ice maker won’t make ice. Often, addressing these simpler issues can restore your machine to optimal functionality without needing to delve into more complex electrical repairs. Remember, regular maintenance and being aware of your machine’s operational requirements can prevent most of these problems. Always refer to your manufacturer’s guidelines for specific maintenance tips and troubleshooting steps.
Conclusion: Wrapping Up
As we have progressed through the intricate process of diagnosing your ice machine, it has become abundantly evident that for the sake of maintenance and repair, it is essential to have a solid grasp of the potential electrical problems. In the event that your countertop ice maker is unable to produce ice due to worn-out components or a more fundamental electrical issue, the methods that have been detailed provide a sound foundation for diagnosing and correcting the issue.
- Recap of Electrical Troubleshooting: We’ve detailed the symptoms and solutions for electrical faults that might stop your ice maker from functioning correctly.
- Importance of Regular Maintenance: Staying proactive with the maintenance of your ice machine can prevent many problems before they start, saving you time and inconvenience.
- Call to Action: Don’t let a malfunctioning ice maker disrupt your daily life or special events. If the troubleshooting steps provided don’t resolve the issue, consider reaching out to a professional for a thorough inspection.
Remember, the key to a reliable ice machine is regular care and prompt attention to any signs of trouble. By keeping an eye on the electrical components and performing routine checks, you can ensure that your ice maker remains a dependable source of refreshment for years to come.
Engage with us in the comments or share your experiences and tips on maintaining and repairing ice machines. We value your insights and look forward to helping you keep your cool, no matter the circumstances.
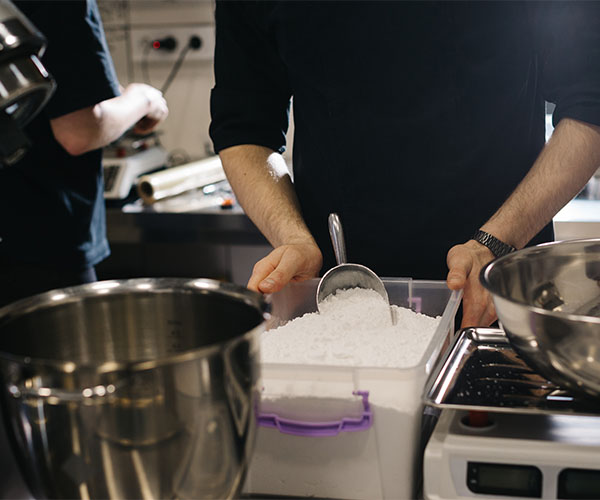
FAQs About Electrical Issues in Ice Machines
1. What are the common signs that electrical issues might be causing my ice machine to malfunction?
- Look for inconsistent ice production, unexpected shutdowns, and failure to start as primary indicators of potential electrical problems.
2. Could a simple power surge damage my ice machine?
- Yes, power surges can harm the electronic components of your ice machine, potentially leading to failures in ice production.
3. What should I check first if my ice machine isn’t making ice?
- Initially, ensure the machine is properly plugged in and receiving power. Check the fuse or circuit breaker connected to the machine.
4. Are there any quick fixes I can try before calling a technician?
- Reset your ice machine by unplugging it for a few minutes, then reconnect it. Also, check and clean any filters or vents, as blocked airflow can mimic electrical issues.
5. How often should electrical components of ice machines be inspected?
- It’s wise to have the electrical systems inspected at least annually by a professional to prevent issues before they start affecting ice production.
6. Can a faulty thermostat cause my ice machine to stop making ice?
- Yes, a malfunctioning thermostat can fail to trigger the ice-making process, as it doesn’t detect the correct temperature required to start production.
7. What DIY maintenance can I perform to avoid electrical problems with my ice machine?
- Regularly clean all accessible parts, ensure electrical connections are tight and free from corrosion, and replace any worn cords or wires.
8. When should I decide to replace my ice machine instead of repairing it?
- Consider replacement if your ice machine is old and repairs are becoming frequent and costly, especially if parts are hard to find or if the unit uses outdated technology that consumes more energy.