Introduction
Any person who has ever been in charge of throwing a party is familiar with the instant dread that comes over them when their reliable ice maker stops producing cubes. Take for example the following scenario: you are around one hour away from the arrival of guests, and your ice machine, which was functioning normally only the day before, suddenly stops making any ice. Although it is making progress, where is the ice? It is not just useful to have an understanding of advanced troubleshooting for your ice machine; it is crucial to have this knowledge because this is a common circumstance that has the potential to ruin any event. In this all-encompassing tutorial, we will go deeply into the mechanics of what could be causing your ice maker to malfunction, and we will offer you with extensive instructions on how to diagnose and repair these problems. Regardless of whether you are an expert in mechanical repair or a newbie in appliance repair, the purpose of this book is to provide you with the knowledge necessary to confront the issue head-on, so assuring that you will never again be without ice. https://amzn.to/3WoePQf
Understanding Your Ice Machine
When tackling the issue of an ice machine running but not making ice, it’s crucial to start with a solid understanding of how these devices operate. This knowledge not only helps in diagnosing the problem but also in effectively communicating with technicians should you need to escalate the issue. Here’s a breakdown of the key components and their functions, which could be impacting your machine’s ability to produce ice:
- Water Inlet Valve: This is the gateway through which water enters your ice machine. If this valve is malfunctioning or blocked, water can’t reach the ice mold, which is essential for ice production.
- Evaporator Plate: This component is responsible for freezing the water into ice. Any issues here can prevent the formation of ice, despite the machine running.
- Thermostat: The thermostat regulates the temperature within the ice machine. If it fails, the evaporator plate might not get cold enough to produce ice or could get too cold, causing other mechanical issues.
Signs and Symptoms of a Malfunctioning Ice Machine:
- No ice production: The most obvious sign. The machine runs, but no ice is made.
- Strange noises: Buzzing or clicking sounds can indicate mechanical failures.
- Water leaks: These could suggest a problem with the water inlet valve or connections inside the machine.
By familiarizing yourself with these components and signs, you can more effectively troubleshoot and communicate the specific issues affecting your ice machine. In the following sections, we will delve deeper into how you can diagnose and address these problems to restore your machine’s ice production capabilities.

Pre-Troubleshooting Steps
Before diving into the nitty-gritty of diagnosing and fixing your ice machine running but not making ice, it’s crucial to set the stage for effective troubleshooting. These preliminary steps will ensure your safety and prepare your ice machine for the in-depth troubleshooting process.
- Safety First:
- Unplug the Machine: Always ensure the ice machine is unplugged before you begin any troubleshooting to avoid any electrical hazards.
- Gather Protective Gear: Wear gloves to protect your hands from sharp edges inside the machine, and consider safety goggles if you plan to use any compressed air or cleaning chemicals.
- Assemble Your Tools:
- Basic Toolkit: Include a screwdriver, pliers, and a flashlight for visibility.
- Multimeter: Essential for testing electrical components to identify where an issue might be occurring.
- Thermometer: To check the temperature inside the ice machine and verify if it’s within the correct range.
- Document the Symptoms:
- Observe and Note Down: Carefully observe the machine’s behavior and jot down any unusual signs or noises. Is the machine running louder than usual? Does the water seem to flow properly?
- Access Diagnostic Codes:
- Check for a Diagnostic Mode: Some modern ice machines have a built-in diagnostic mode that can be activated according to the user manual. This mode can provide error codes that pinpoint specific issues.
- Record All Displayed Codes: Any error codes displayed can be crucial for pinpointing the exact problem without guesswork.
- Review the User Manual:
- Manufacturer’s Guidelines: Always check the user manual for specific troubleshooting steps recommended by the manufacturer. This manual may also offer insights into common issues specific to your model.
- Warranty Information: Be aware of the warranty conditions as some troubleshooting steps might void the warranty.
- Prepare the Workspace:
- Clear Area: Ensure you have a clean and unclipped workspace around your ice machine. Moving it to a more accessible spot might be necessary to reach all its parts easily.
- Lighting: Good lighting is crucial; make sure your workspace is well-lit to avoid any missed cues on the machine’s condition.
Taking these initial steps will not only prepare you for a smoother troubleshooting process but also ensure that you are doing it safely and efficiently. Understanding your ice machine’s layout, capabilities, and symptoms will greatly enhance your ability to diagnose and resolve issues, getting it back to producing ice in no time.
Diagnostic Procedures
When faced with the all-too-common problem of an ice machine running but not making ice, diving into diagnostic procedures is your next best step. These steps will help you understand what’s going wrong inside your machine and guide you on how to fix it. Here’s how to methodically approach the diagnostic process: https://amzn.to/3WoePQf
- Accessing Diagnostic Codes:
- Most modern ice machines come with a digital diagnostic panel. If available, refer to your machine’s user manual to locate and interpret these codes.
- Diagnostic codes can swiftly pinpoint areas of concern, such as issues with temperature sensors or water supply, making them invaluable in troubleshooting.
- Manual Testing of Key Components:
- Water Inlet Valve: Check if the valve is receiving power and if it’s physically blocked or clogged. A multimeter can confirm electrical continuity; a lack thereof suggests a need for replacement.
- Evaporator Plate: This component is crucial for ice formation. Inspect for signs of damage or mineral build-up, which can hinder its function.
- Using a Multimeter to Check Electrical Issues:
- Safety First: Always ensure the machine is unplugged before attempting any electrical testing.
- Set your multimeter to the continuity setting and test the heating element and thermostat. Lack of continuity indicates a need for replacement.
- Check for any faulty or loose wiring that could be causing operational issues, especially those related to the machine’s ability to freeze water.
By systematically following these diagnostic steps, you can pinpoint specific problems affecting your ice machine. This process not only saves time but also directs you towards the most effective solution, whether it’s a simple repair or a part replacement. Understanding and applying these procedures will ensure that your ice machine returns to optimal performance swiftly, keeping you prepared for any event or daily need without disruption.
Remember, effective troubleshooting is methodical and patient, so take your time to understand each step and how it relates to the overall functioning of your ice machine.
Common Problems and Solutions
When your countertop ice maker won’t make ice, several issues could be at fault, from simple fixes to more complex mechanical malfunctions. Here’s a closer look at the common problems that might be causing this frustrating issue and practical solutions to get your machine back up and running:
- Water Flow Problems
- Blocked water filters: Over time, water filters can become clogged with sediment and minerals, restricting flow to the ice maker. Check your filter and replace it if necessary.
- Frozen water lines: Occasionally, the lines feeding water into your ice maker can freeze, particularly in colder environments or if the freezer settings are too high. Thaw these lines carefully with a hair dryer or by gently warming the surroundings.
- Faulty water inlet valve: If the valve that supplies water to your ice maker is malfunctioning, it won’t deliver the necessary water to produce ice. Test the valve with a multimeter to see if it needs replacing.
- Temperature Inconsistencies
- Malfunctioning thermostat: A thermostat that isn’t reading temperatures accurately can prevent your ice maker from triggering its ice production cycle. Use a thermometer to monitor your freezer’s temperature and adjust the thermostat accordingly.
- Refrigerant issues: Low refrigerant levels or leaks can impair the cooling ability of your ice maker, preventing it from producing ice. This is a more complex issue that typically requires a professional technician.
- Mechanical Failures
- Worn out pump: The pump that circulates water over the evaporator plate might be failing. Listen for unusual noises or check for a weak water flow, which can indicate a problem with the pump.
- Damaged evaporator plate: If the evaporator plate is damaged or has significant wear and tear, it may not freeze the water effectively. Inspect the plate for signs of damage or corrosion.
- Motor issues: The motor powers the mechanical parts of the ice maker. If it’s overheating or producing a burning smell, it may need repair or replacement.
Addressing these issues can help resolve the problem when your countertop ice maker won’t make ice. Each solution is designed to tackle a specific part of the ice making process, ensuring that every component functions as intended. Remember, when dealing with refrigerant issues or electrical components, it may be safer and more effective to consult with a professional.
If these troubleshooting steps don’t resolve the problem, it could indicate a more serious issue that might require professional assessment and repair. Regular maintenance and timely replacement of components like water filters and cleaning of accessible parts can prevent many of these issues and extend the life of your ice maker.
By understanding these common problems and solutions, you can become more proficient in maintaining your ice machine, ensuring it operates efficiently and continues to serve your needs without interruption.
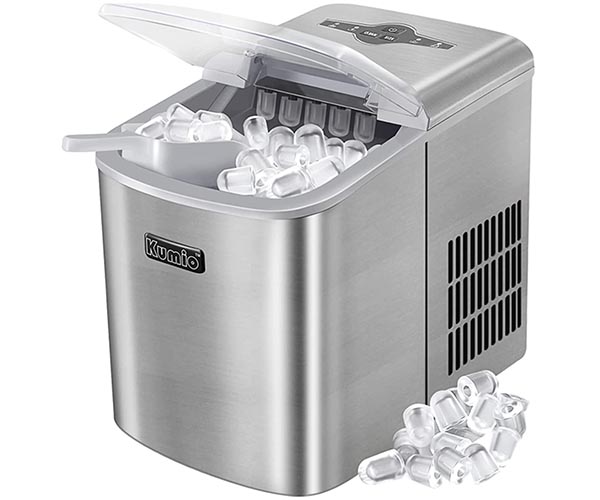
When to Call a Professional
Troubleshooting your countertop ice maker when it won’t make ice can often be handled with a bit of DIY spirit and the right guidance. However, there are certain situations where calling a professional is not only recommended but necessary. Understanding when to seek professional help can save you both time and the potential cost of further damaging your appliance. Here are some key indicators that it’s time to call in an expert: https://amzn.to/3WoePQf
- Persistent Problems Despite Troubleshooting: If you’ve followed all the advanced troubleshooting steps and your ice maker still isn’t producing ice, this could indicate a deeper, possibly electrical or mechanical, issue that requires professional expertise.
- Refrigerant Issues: Dealing with refrigerant, such as leaks or refilling, is something that should only be handled by a certified technician due to the technical knowledge required and potential health risks.
- Water Leaks: If you notice water leaking significantly around your machine, it could be due to issues with internal components that are not easily accessible or repairable without detailed knowledge of the machine’s design.
- Electrical Faults: Any signs of electrical issues, such as sparks, burnt smells, or consistent power failures, warrant immediate professional attention to prevent safety hazards.
- Warranty Concerns: Check if your ice maker is still under warranty. Attempting repairs yourself can sometimes void warranties, so if your machine is covered, let qualified service professionals handle the repairs.
Reasons to Prioritize Professional Help:
- Safety: Handling electrical components and refrigerants can be dangerous without proper training.
- Cost-Effectiveness: Incorrect DIY repairs can lead to more significant damage, potentially resulting in higher costs down the line.
- Time-Saving: Professionals can diagnose and fix issues more quickly due to their expertise and tools.
Finding a Qualified Technician:
- Research: Look for service providers with good reviews and verify their certifications to ensure they are qualified to work on your specific model of ice maker.
- References: Ask for recommendations from friends or family who have had similar repairs done.
- Compare Quotes: Get multiple estimates from different technicians to ensure you are getting a fair price for the repair work.
By understanding when to call a professional and ensuring you choose the right one, you can get your countertop ice maker back to making ice efficiently and safely. Remember, the goal is to fix the problem effectively, not just quickly, to ensure your appliance operates well for years to come.
Maintenance Tips to Prevent Future Issues
Maintaining your ice machine properly can prevent many common issues from arising, including the frustrating scenario when your countertop ice maker won’t make ice. Here are some preventative maintenance tips to help keep your ice machine in top working condition:
- Regular Cleaning: It’s essential to clean your ice machine regularly to prevent build-up that can clog the system. Follow the manufacturer’s instructions for the correct cleaning procedure and frequency.
- Inspect Water Filters: Regularly check and replace the water filters according to the manufacturer’s recommendations. Clean water is crucial for both ice quality and machine performance.
- Check Water Flow: Ensure that the water inlet valve is free from obstructions and functioning correctly. Poor water flow can result in insufficient ice production.
- Monitor Temperature Settings: The environment where your ice machine operates should have a stable temperature. Fluctuations can affect the machine’s efficiency and ice quality.
- Regularly Inspect Seals and Hoses: Check for leaks or worn out seals and hoses. These can lead to water leakage and affect the ice making process.
- Avoid Overloading: Do not overload the machine with more water than recommended. This can stress the system and lead to malfunction.
- Schedule Professional Inspections: Even with diligent personal maintenance, it’s wise to have your ice machine professionally inspected at least once a year to ensure all mechanical parts are in good working order.
- Keep the Area Around Your Ice Machine Clear: Ensure that the area around your ice machine is clear of debris and dust, which can get into the machine and cause issues.
- Use the Right Accessories: Only use accessories recommended by the manufacturer, such as scoops and cleaning agents, to avoid damaging your machine.
- Educate All Users: Make sure everyone who uses the ice machine knows the correct operation procedures to prevent misuse and potential damage.
Following these steps diligently can greatly increase the lifespan of your ice machine and decrease the chances of facing an issue where your countertop ice maker won’t make ice. Regular maintenance not only helps in preventing breakdowns but also ensures you are always ready for any gathering without a last-minute ice emergency.
Conclusion
As we wrap up this in-depth guide on troubleshooting your ice machine, remember that the difference between a quick fix and a persistent problem often lies in a thorough understanding of the device. Countertop ice maker not freezing? This could point to several issues—from simple fixes to more complex mechanical failures. Here are some final thoughts to keep in, mind:
- Prevention is Key: Regular maintenance isn’t just a recommendation; it’s a necessity to prevent common issues like your ice maker not freezing.
- Knowledge is Power: Understanding the signs of potential problems can save you time and money. Recognizing symptoms early can prevent the inconvenience of a non-functional ice maker during crucial times.
- When to Seek Help: If the troubleshooting steps provided have been followed without success, it may be time to call in a professional. This doesn’t mean you’ve failed; some problems simply require expert hands.
Above all, don’t let frustration get the better of you. Use this guide as a starting point, and remember that every problem is an opportunity to learn more about your appliance. With the right approach, you can extend the life of your ice machine and ensure it remains a reliable part of your kitchen arsenal.
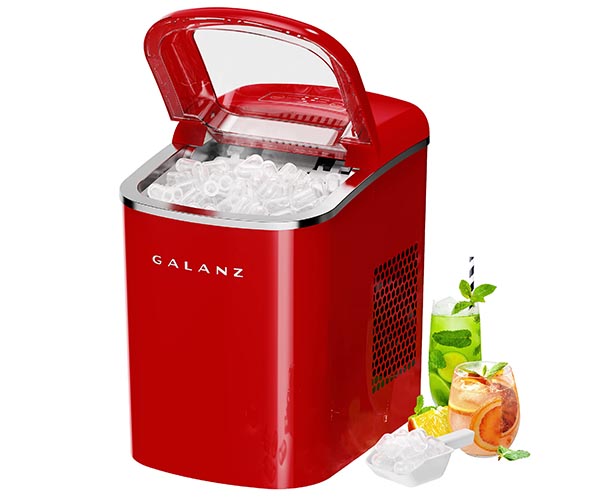
FAQs: Advanced Troubleshooting for Ice Machines
- What should I check first if my ice machine isn’t freezing?
- First, ensure that your machine is getting adequate water flow and that the water filter isn’t clogged. Check the supply valve and filter for any blockages or damage.
- Why is my ice machine running but not producing ice?
- This could be due to a few issues such as a malfunctioning thermostat, low refrigerant levels, or issues with the evaporator coil. Start by checking the thermostat settings and ensure it’s not set too high.
- How can I tell if the water inlet valve is faulty?
- If the water inlet valve is faulty, the machine will have trouble filling the ice mold. You can test the valve’s function with a multimeter to see if it has continuity.
- What are the signs of a refrigerant leak in my ice machine?
- Signs of a refrigerant leak include ice forming on the compressor, unusually warm internal temperatures, or a noticeable decrease in ice production. You might also hear a hissing sound from leaking gas.
- Can I fix a broken evaporator on my own?
- Fixing a broken evaporator can be complex and generally requires professional help, especially since it involves handling refrigerant.
- What regular maintenance should I perform to avoid troubleshooting?
- Regularly clean the machine’s filters and interior, check and tighten electrical connections, and inspect the condenser and evaporator for ice buildup or dust.
- How do I reset my ice machine?
- Most ice machines can be reset by turning them off, unplugging them from their power source, waiting a few minutes, and then plugging them back in. Check your manual for model-specific instructions.
- What should I do if advanced troubleshooting doesn’t solve the problem?
- If advanced troubleshooting doesn’t resolve the issue, it’s advisable to contact a professional technician. Make sure they are certified and have experience with your particular model of ice machine.
Each of these points delves into the common issues you may encounter with your ice machine and provides a starting point for troubleshooting. Always refer to your specific model’s user manual for detailed instructions and safety information.