Introduction
Portable ice makers are a fantastic addition to any home, offering the convenience of ice production without the need for a permanent installation. Whether for parties, camping trips, or everyday use, these compact appliances provide a steady supply of ice at the touch of a button. However, like all machines, they require regular maintenance and occasional repairs to keep functioning optimally. This guide aims to be your go-to resource for diagnosing and fixing common issues with portable ice makers, ensuring you can keep the ice flowing without interruption.
Understanding Your Portable Ice Maker
To effectively perform countertop ice maker repair, it’s essential to understand the different types of portable ice makers and their key components. This knowledge will help you diagnose and fix issues accurately, ensuring your ice maker functions optimally. https://amzn.to/3WoePQf
Types of Portable Ice Makers
There are three main types of portable ice makers, each with unique characteristics and uses:
- Nugget Ice Makers: These machines produce soft, chewable ice nuggets that are popular in restaurants and bars. Nugget ice, also known as “Sonic ice,” is ideal for cocktails and soft drinks due to its texture and ability to absorb flavors.
- Bullet Ice Makers: These units create cylindrical ice cubes with a hollow center. Bullet ice is quick to produce and perfect for everyday use in beverages. The shape and size of the ice cubes make them versatile and suitable for various drinks.
- Flake Ice Makers: These machines generate small, soft ice flakes that are excellent for food presentation and preservation. Flake ice is commonly used in grocery stores, seafood markets, and for medical applications due to its cooling efficiency and moldability.
Key Components
A thorough understanding of the key components of a portable ice maker is crucial for effective repair and maintenance. Here are the primary parts you need to be familiar with:
- Compressor: The compressor powers the cooling system, which is essential for ice production. It compresses the refrigerant and circulates it through the coils, facilitating the freezing process.
- Evaporator: The evaporator is responsible for converting the refrigerant from liquid to gas. This process absorbs heat and produces ice. Any issues with the evaporator can lead to inefficient ice production or complete failure.
- Water Pump: The water pump circulates water from the reservoir to the freezing area. It ensures that a consistent water supply reaches the evaporator. Problems with the water pump can result in no ice or irregular ice production.
- Control Module: The control module manages the entire ice-making process, ensuring all components work in sync. It regulates the timing, water flow, and temperature settings. A malfunctioning control module can disrupt the entire system.
Understanding these components and their functions will empower you to troubleshoot and perform countertop ice maker repair effectively. By recognizing the signs of malfunction in each part, you can take the appropriate steps to fix the issues and maintain your ice maker’s performance.
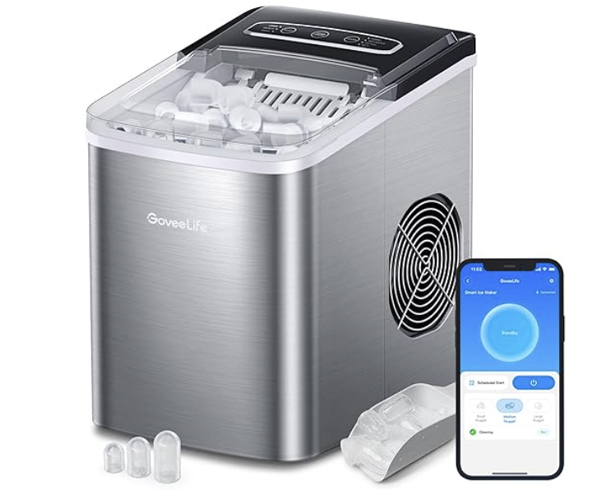
Common Issues and Diagnostics
No Ice Production
Experiencing no ice production from your countertop ice maker can be frustrating. Here are some steps to diagnose and fix the issue:
- Check power supply and connections: Ensure your ice maker is plugged in and receiving power. Check the outlet by plugging in another device to confirm it’s working. Inspect the power cord for any damage.
- Inspect water supply and filter: Verify that the water reservoir is full. A low water level can halt ice production. Also, check if the water filter is clogged or needs replacement, as a blocked filter can restrict water flow.
Slow Ice Production
If your countertop ice maker is producing ice too slowly, it may be due to environmental factors or maintenance issues.
- Examine ambient temperature and airflow: Ice makers perform best in cool environments. Ensure the unit is placed in a well-ventilated area away from heat sources. The ideal room temperature should be between 50°F and 90°F.
- Assess cleanliness of condenser coils: Dirty condenser coils can impede the cooling process. Clean the coils regularly using a soft brush or vacuum to remove dust and debris.
Poor Ice Quality
Poor ice quality, such as cloudy or off-tasting ice, can be indicative of underlying problems with your ice maker.
- Investigate water quality and filtration: Use filtered or distilled water to improve ice clarity and taste. Tap water with high mineral content can affect ice quality. Replacing the water filter regularly can also help.
- Look for signs of mold or mineral buildup: Inspect the interior of the ice maker for any mold or mineral deposits. Clean the machine thoroughly using a mixture of vinegar and water to remove any buildup and sanitize the surfaces.
By addressing these common issues, you can keep your countertop ice maker running efficiently and producing high-quality ice. Regular maintenance and timely repairs are essential to prolong the lifespan of your appliance and ensure consistent performance. https://amzn.to/3WoePQf
Step-by-Step Repair Guide
Tools and Materials Needed
To successfully repair your countertop ice maker, you’ll need a few essential tools and materials:
- Basic tool kit: Screwdrivers, pliers, wrenches, and other common tools.
- Replacement parts: Specific to your ice maker model, such as filters or compressors.
- Cleaning supplies: Mild detergent, soft cloths, and descaling solution.
Diagnosing the Problem
Before diving into repairs, it’s crucial to accurately diagnose the issue. Here are some detailed troubleshooting steps:
- No Ice Production:
- Verify the power supply: Ensure the ice maker is plugged in and switched on.
- Check the water supply: Confirm that the reservoir is filled and the water filter is clean.
- Slow Ice Production:
- Ambient temperature and airflow: Make sure the unit is in a cool, ventilated area.
- Condenser coils: Inspect and clean the coils to ensure efficient cooling.
- Poor Ice Quality:
- Water quality: Use filtered water to avoid mineral buildup.
- Signs of mold or minerals: Regularly clean the ice maker’s interior.
For a visual aid, consider creating flowcharts for common issues to streamline the diagnostic process.
Repair Procedures
Once you’ve identified the problem, follow these repair procedures to fix your countertop ice maker:
Replacing the Water Filter
- Turn off the ice maker and unplug it from the power source.
- Locate the water filter: Refer to your user manual for the exact location.
- Remove the old filter: Turn it counterclockwise to release it.
- Install the new filter: Align it properly and turn clockwise until secure.
- Run a cleaning cycle: This helps to clear any debris from the new filter.
Cleaning the Condenser Coils
- Unplug the ice maker and move it to a well-ventilated area.
- Access the coils: Usually located at the back or bottom of the unit.
- Vacuum or brush away dust: Use a soft brush or vacuum to remove dust and debris.
- Wipe with a damp cloth: Ensure the coils are clean and free from obstructions.
Fixing a Faulty Compressor
- Disconnect the ice maker from the power supply.
- Locate the compressor: Typically found at the back of the unit.
- Test the compressor: Use a multimeter to check for continuity.
- Replace the compressor: If faulty, follow the manufacturer’s instructions for replacement.
Adjusting the Thermostat
- Identify the thermostat: Refer to your ice maker’s manual.
- Adjust the setting: Turn the thermostat to the desired temperature.
- Monitor the ice production: Ensure the adjustments yield the correct ice quality and quantity.
Replacing the Control Module
- Turn off the unit and unplug it.
- Remove the control panel cover: Access the control module.
- Disconnect the old module: Carefully detach the wiring.
- Install the new module: Connect the wiring and secure the module in place.
- Test the unit: Plug in the ice maker and run a cycle to ensure functionality.
By following these steps, you can troubleshoot and repair most common issues with your countertop ice maker. Regular maintenance and timely repairs will extend the life of your appliance and ensure a continuous supply of ice.
Additional Tips
- Regular cleaning: Clean your ice maker regularly to prevent mold and mineral buildup.
- Proper storage: Store your ice maker correctly during off-seasons to avoid damage.
- Routine inspections: Periodically check for wear and tear to catch problems early.
Remember, while some repairs can be done at home, more complex issues might require professional assistance. If you’re unsure, it’s always best to consult with a qualified technician. This guide aims to provide you with the knowledge to keep your countertop ice maker running smoothly and efficiently.
Conclusion: Keeping your countertop ice maker in good working condition is essential for its longevity and performance. By following this guide, you can address common problems and perform necessary repairs, ensuring a steady supply of ice whenever you need it. Feel free to share this guide with others and provide feedback to help improve it further.
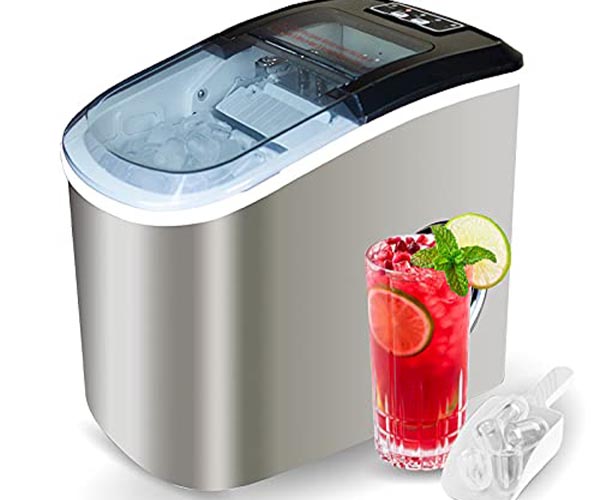
Preventative Maintenance Tips
Maintaining your portable ice maker ensures longevity and optimal performance. Regular cleaning and inspections are crucial. Here are some preventative maintenance tips to keep your ice maker running smoothly.
Regular Cleaning Schedule
A thorough cleaning schedule helps prevent buildup and ensures ice quality.
- Daily Tasks:
- Empty the ice bin and dry it to prevent mold.
- Wipe down the exterior with a damp cloth.
- Weekly Tasks:
- Clean the water reservoir with a mild detergent.
- Inspect and clean the ice molds.
- Monthly Tasks:
- Run a cleaning solution through a cycle.
- Check and clean the condenser coils to prevent dust accumulation.
Proper Storage
When your ice maker is not in use, especially during off-seasons, proper storage is vital.
- Tips for Off-Season Storage:
- Drain all water from the reservoir to avoid bacteria growth.
- Clean and dry all parts thoroughly.
- Store in a cool, dry place away from direct sunlight.
- Cover the unit to protect it from dust.
Routine Inspections
Regular inspections help identify issues early, preventing major breakdowns.
- Checking for Wear and Tear:
- Inspect hoses and seals for cracks or leaks.
- Check the power cord for any signs of damage.
- Ensuring Optimal Performance:
- Verify that the thermostat is functioning correctly.
- Ensure that the ice maker is level to avoid water leaks.
Conclusion
By following these preventative maintenance tips, you can avoid common issues and extend the life of your portable ice maker. Regular cleaning, proper storage, and routine inspections are essential. Keeping up with these tasks ensures your ice maker remains efficient and reliable. For more detailed guidance, consult your ice maker’s manual and consider professional maintenance services if needed. Remember, a well-maintained ice maker provides better performance and longevity, saving you time and money in the long run. https://amzn.to/3WoePQf
When to Call a Professional for Your Portable Ice Maker Repair
Understanding when to seek professional help for countertop ice maker troubleshooting can save you time, money, and potential frustration. While many minor issues can be resolved with a bit of DIY effort, there are certain complex repairs best left to the experts.
Complex Repairs
- Issues with Refrigerant Levels
- Refrigerant is crucial for the cooling process in ice makers. Low refrigerant levels can indicate a leak or other underlying issues. Handling refrigerants requires specific tools and expertise due to their hazardous nature. If you suspect a refrigerant problem, it’s safer and more efficient to call a professional.
- Electrical Problems
- Electrical issues, such as faulty wiring or problems with the control board, can be dangerous to address without proper knowledge. These components are integral to the operation of your ice maker and mishandling them can lead to further damage or even safety hazards. An experienced technician can diagnose and fix these problems safely.
Cost vs. Benefit Analysis
When deciding whether to repair or replace your portable ice maker, it’s important to weigh the costs and benefits carefully.
- Repair Costs vs. Replacement Costs
- Consider the cost of the repair compared to the price of a new unit. If the repair cost is more than half the price of a new ice maker, it might be more economical to invest in a replacement. This is especially true for older models that might not be as energy-efficient or reliable as newer ones.
- Evaluating the Age and Condition of the Ice Maker
- Assess the overall condition and age of your ice maker. If your unit is relatively new and in good shape aside from the current issue, repairing it might be worthwhile. However, if it’s old and showing signs of wear and tear, replacing it might be the better option. Newer models often come with improved features and energy efficiency, making them a good long-term investment.
By carefully evaluating these factors, you can make an informed decision about whether to repair or replace your ice maker. Remember, for complex repairs involving refrigerants or electrical components, it’s always best to call a professional. This not only ensures your safety but also guarantees that the repair is done correctly, prolonging the life of your appliance.
If you ever find yourself in doubt, don’t hesitate to consult with a professional who can provide expert advice tailored to your specific situation. They can help you determine the most cost-effective and safe course of action, ensuring your countertop ice maker troubleshooting efforts are successful.
Conclusion
Summary of Key Points
- Portable ice makers are a convenient solution for home use, providing a steady supply of ice.
- Regular maintenance and timely repairs are crucial to keep these appliances running efficiently.
- Understanding common issues like no ice production, slow ice production, and poor ice quality can help in diagnosing and fixing problems.
- Preventative maintenance, such as regular cleaning and proper storage, extends the lifespan of your ice maker.
- Knowing when to call a professional for complex repairs can save time and money.
Encouragement to Maintain Regular Upkeep
Regular upkeep of your portable ice maker not only ensures optimal performance but also prolongs its life. By following the steps outlined in this guide, you can address issues promptly and prevent minor problems from becoming major repairs. Keep a maintenance schedule and perform routine checks to catch any wear and tear early. This proactive approach will save you time, money, and the inconvenience of a malfunctioning ice maker.
Invitation to Share the Guide with Others and Provide Feedback
We hope this guide on countertop ice maker troubleshooting has been helpful. If you found this information valuable, please share it with friends and family who might benefit from it. Your feedback is also important to us. Let us know if there are areas we can improve or additional topics you would like us to cover. Together, we can ensure that everyone enjoys the convenience of a well-maintained portable ice maker.
By following these tips and maintaining your ice maker regularly, you’ll ensure a steady supply of ice for all your needs. Share this comprehensive guide and contribute to a community of well-informed ice maker owners. Your insights and experiences can help others, so don’t hesitate to provide feedback and engage with us.
Maintaining a countertop ice maker doesn’t have to be daunting. With the right knowledge and a proactive approach, you can keep your appliance in top condition. Thank you for reading, and happy ice making!
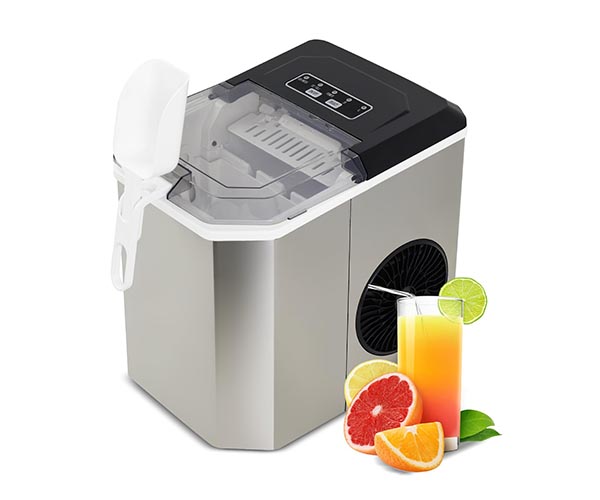
FAQs About Portable Ice Maker Repair Guide
1. What are the most common issues with portable ice makers?
The most common issues include:
- No ice production: This can be due to power supply issues, water supply problems, or clogged filters.
- Slow ice production: Often caused by high ambient temperatures, poor airflow, or dirty condenser coils.
- Poor ice quality: This can result from using impure water, mold, or mineral buildup inside the machine.
2. How can I troubleshoot a portable ice maker that isn’t producing ice?
To troubleshoot a portable ice maker that isn’t producing ice, follow these steps:
- Check the power supply and ensure the machine is plugged in.
- Inspect the water reservoir and ensure it is filled.
- Clean or replace the water filter.
- Ensure the machine is in a cool, well-ventilated area.
3. What tools and materials do I need for basic repairs on a portable ice maker?
For basic repairs, you will need:
- A basic tool kit (screwdrivers, pliers, etc.)
- Replacement parts specific to your ice maker model
- Cleaning supplies like a soft cloth, mild detergent, and descaling solution
- A water filter, if needed
4. How often should I clean my portable ice maker?
You should clean your portable ice maker:
- Daily: Wipe down the exterior and remove any ice.
- Weekly: Clean the water reservoir and the ice basket.
- Monthly: Deep clean the machine, including the condenser coils and any internal components as recommended by the manufacturer.
5. Can I use tap water in my portable ice maker?
While you can use tap water, it is recommended to use filtered or distilled water to prevent mineral buildup and improve the quality of the ice. Using impure water can lead to poor ice quality and frequent cleaning requirements.
6. What should I do if my ice maker has a bad smell?
If your ice maker has a bad smell:
- Clean the machine thoroughly, including the water reservoir and ice basket.
- Use a descaling solution to remove any mineral buildup.
- Ensure the water filter is clean or replace it if necessary.
- Use fresh, filtered water for making ice.
7. When should I call a professional for ice maker repairs?
Call a professional when:
- The ice maker has refrigerant issues or electrical problems.
- You’ve attempted basic troubleshooting and the issue persists.
- The cost of repair parts and your time outweighs the benefits of fixing it yourself.
- The machine is still under warranty and you want to avoid voiding it by attempting repairs yourself.
8. How can I prevent my portable ice maker from breaking down?
Prevent breakdowns by:
- Regularly cleaning the machine and following a maintenance schedule.
- Using filtered or distilled water to prevent mineral buildup.
- Ensuring the machine is kept in a cool, well-ventilated area.
- Performing routine inspections to check for wear and tear and addressing issues promptly.
By following these FAQs, you can better understand how to maintain and repair your portable ice maker, ensuring it continues to produce high-quality ice efficiently.