Introduction
When you find yourself needing a cold beverage, only to find out that your ice maker has ceased manufacturing ice, have you ever experienced this experience? Not only does this typical problem cause disruptions to your regular routine, but it may also be an indication of more serious problems within your ice machine that require immediate care. We are going to go over the basic actions that you need to perform when your ice machine is active but not producing ice in this detailed tutorial that we have prepared for you. The purpose of this post is to provide you with the knowledge necessary to identify and fix the problem in a timely manner. This knowledge will range from fundamental inspections of the power and water supply to more in-depth troubleshooting of frequent mechanical faults. The following instructions will assist you in ensuring that your ice machine is back in operation with minimal downtime, regardless of whether you are a homeowner or the manager of a business that is dependent on a consistent supply of ice. https://amzn.to/3WoePQf
Initial Checks
When faced with the frustrating scenario where your ice machine is running but not making ice, it’s crucial to start with some basic yet essential checks. These preliminary steps can help pinpoint the root of the problem without needing advanced tools or technical knowledge. Let’s walk through the key initial checks you should perform:
- Power Supply and Settings
- Ensure that your ice machine is connected to a power source and is turned on. Occasionally, connections can loosen or power outlets can fail.
- Verify that the machine’s settings are configured correctly. Incorrect settings can prevent ice production even though the machine appears to be running.
- Water Supply Check
- Check the water inlet valve for any obstructions or kinks in the hose that could restrict water flow to your ice machine.
- Ensure that the water pressure to the machine is adequate. Low water pressure can hinder the machine’s ability to produce ice.
By methodically going through these checks, you can often resolve simple issues that may be causing your ice machine to run without producing ice. If these steps don’t solve the problem, further troubleshooting will be necessary to delve into more complex issues. Remember, consistent maintenance and regular checks can prevent many common problems associated with ice machines.
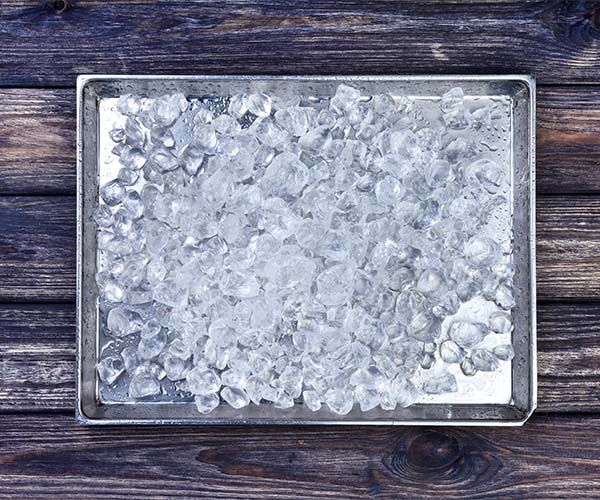
Common Problems and How to Troubleshoot Them
When your countertop ice maker won’t make ice, the frustration can quickly set in. However, several common issues can cause this problem, and with a bit of troubleshooting, you can often resolve them yourself. Here’s a detailed look at what might be going wrong and how to fix it:
- Frozen Water Lines:
- Symptoms: No water flows into the ice mold, or water trickles in slowly.
- Solution: Unplug the ice maker, locate the water lines, and inspect them for frost or ice buildup. If you find any, gently warm the lines with a hair dryer to thaw them.
- Clogged Filters:
- Symptoms: Low water flow that affects ice production.
- Solution: Check the filter for any sediment or impurities that might be blocking water flow. Most ice makers have a removable filter that can be cleaned or replaced. If your filter is old or heavily clogged, replace it to restore proper water flow.
- Sensor Failures:
- Symptoms: The ice maker fails to cycle correctly, or continues to run without producing ice.
- Solution: Locate the sensor near the water tray or ice mold. Use a multimeter to check for continuity. If the sensor is defective (no continuity), replace it to ensure the ice maker cycles correctly.
- Mechanical Malfunctions:
- Symptoms: Unusual noises, the ice maker runs continuously without ejecting ice, or ejects partially formed ice cubes.
- Solution: Inspect mechanical components like the ejector motor or gear assembly. Lubricate moving parts if they are sticking or replace worn-out parts that are causing operational issues.
Understanding these issues and how to tackle them will not only save you time and money but also extend the life of your ice maker. Regular maintenance and prompt attention to small issues will keep your machine running efficiently, ensuring you’re never without ice when you need it most.
Step-by-Step Guide to Basic Fixes
When your countertop ice maker won’t make ice, a few basic troubleshooting steps can be immensely helpful. Below is a detailed guide on how to declog and clean the unit, reset its settings, and optimize the temperature for ice production. Following these steps carefully will help address the most common issues that prevent ice makers from functioning properly.
- Declogging and Cleaning:
- Inspect the Water Lines: First, ensure that there are no kinks or clogs in the water supply line. A blocked water line can impede the flow of water necessary for ice production.
- Clean the Filter: Regularly cleaning or replacing the air filter is crucial as a dirty filter can restrict airflow and impair the ice maker’s performance.
- Check the Drain Cap: Make sure the drain cap is securely in place. A loose drain cap can lead to water leakage and affect ice production.
- Reset Procedures:
- Power Cycle the Ice Maker: Unplug your ice maker for a few minutes before plugging it back in. This can reset the machine’s internal computer and solve temporary software glitches.
- Consult the Manual for Reset Instructions: Some models have a reset button or a specific procedure to follow. Refer to your user manual for detailed instructions.
- Temperature Adjustments:
- Check Environment Temperature: Ice makers function optimally within specific temperature ranges. Ensure the ambient temperature is suitable for your model.
- Adjust the Thermostat: If your ice maker has a visible thermostat dial, try adjusting it to see if it affects ice production. Lower temperatures typically promote faster ice production.
These steps are designed to resolve the basic issues when your countertop ice maker won’t make ice. Regular maintenance and timely troubleshooting can save you from bigger repairs and ensure your ice maker continues to function efficiently.
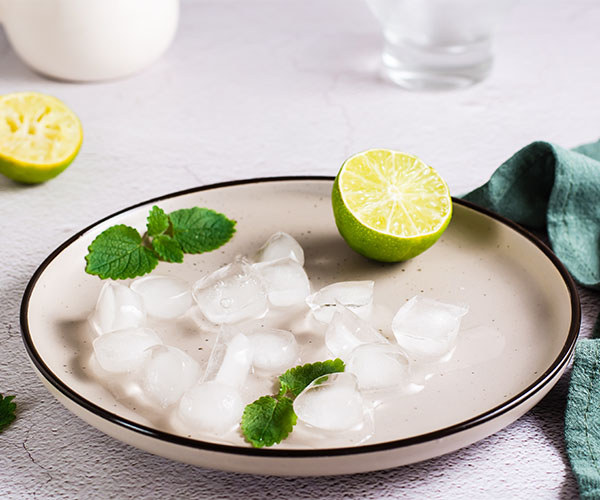
When to Call a Professional
While many issues with a countertop ice maker not freezing can be resolved through basic troubleshooting, there are situations where calling a professional is the best course of action. Understanding when to seek expert help can save you both time and the risk of further damaging your machine. Here are some scenarios where professional assistance is necessary:
- Persistent Issues Despite Basic Troubleshooting: If your ice maker continues to malfunction despite following all the initial troubleshooting steps, it’s time to call in the pros.
- The machine runs, but no ice is produced.
- Frequent error messages that are not resolved by resetting the machine.
- Electrical Problems: Any issues that seem electrical in nature should be handled by a qualified technician, especially if you notice:
- Flickering lights on the machine’s panel.
- Unusual noises that suggest a mechanical failure.
- Leaks and Water Damage: Water leaks can cause significant damage to your ice maker and your property. Professional help is needed when:
- You notice water pooling around the machine.
- There are signs of water damage inside the machine, which could lead to mold growth.
- Complex Mechanical Failures: Some components of an ice maker are complex and require specialized knowledge to repair or replace. These include:
- Compressor issues.
- Refrigerant leaks or problems with the coolant system.
- Warranty and Service Considerations: Before attempting any DIY repairs, check if your ice maker is still under warranty. Professional servicing might be covered, which can include:
- Free or discounted repair services.
- Replacement parts at no extra cost.
Calling a professional not only ensures that your countertop ice maker is repaired effectively but also helps maintain its longevity and efficiency. If you’re unsure about the nature of the problem, consulting with a technician can provide peace of mind and prevent further complications.
Remember, the goal is to get your ice maker back to its optimal condition with minimal hassle. If the troubleshooting steps seem overwhelming or if the machine shows signs of significant wear and damage, it’s time to reach out to a professional repair service. https://amzn.to/3WoePQf
Preventative Maintenance Tips
Maintaining your ice machine properly not only ensures a consistent supply of ice but also prevents the common issue where the ice machine is running but not making ice. Here’s a detailed guide to help you keep your ice machine in peak condition:
- Regular Cleaning and Sanitization:
- Ensure that you clean and sanitize your ice machine every six months. This involves removing any mineral build-ups and sanitizing all surfaces that come in contact with water or ice.
- Focus on areas like the water filter, ice-making tray, and storage bin which can harbor bacteria and impurities that could clog your system.
- Inspect and Replace Water Filters Regularly:
- Check the water filter every three to six months, depending on your usage and the hardness of your water. A clogged or dirty filter can restrict water flow, leading to ice machine running but not making ice.
- Replace filters as recommended by the manufacturer to ensure clean, clear, and taste-free ice.
- Check and Maintain Water Flow:
- Regularly inspect water lines for kinks, leaks, or blockages. Adequate water flow is crucial for ice production. Reduced water flow can result in smaller or malformed ice cubes, or no ice at all.
- Ensure that the water inlet valve is fully open and functioning correctly.
- Monitor and Adjust the Freezer Temperature:
- The freezer temperature should be set correctly to optimize ice production. If the freezer is too warm, the machine will struggle to produce ice.
- Use a thermometer to check the internal temperature and adjust the settings accordingly to maintain the optimal temperature recommended by the manufacturer.
- Seasonal Adjustments:
- Be aware of the environment where your ice machine operates, especially if it’s subject to seasonal changes. High temperatures during summer can affect the efficiency of your ice machine.
- Adjust the environmental conditions such as cooling and ventilation to ensure that your machine operates within the optimal temperature range.
- Regularly Check for Wear and Tear:
- Inspect mechanical components such as motors, pumps, and gears regularly for signs of wear or damage. Early detection of mechanical issues can save costly repairs and downtime.
- Schedule a professional inspection if you suspect any potential problems.
- Educate Your Team:
- If your ice machine is in a commercial setting, make sure all staff are trained on basic maintenance procedures and understand the signs of potential issues.
- Having knowledgeable staff can help prevent misuse and ensure quick action is taken if the machine stops making ice.
Following these tips will not only help you maintain your ice machine but also prevent the frustrating problem when your ice machine is running but not making ice. Regular maintenance keeps your machine running efficiently and extends its lifespan, saving you money and inconvenience in the long run.
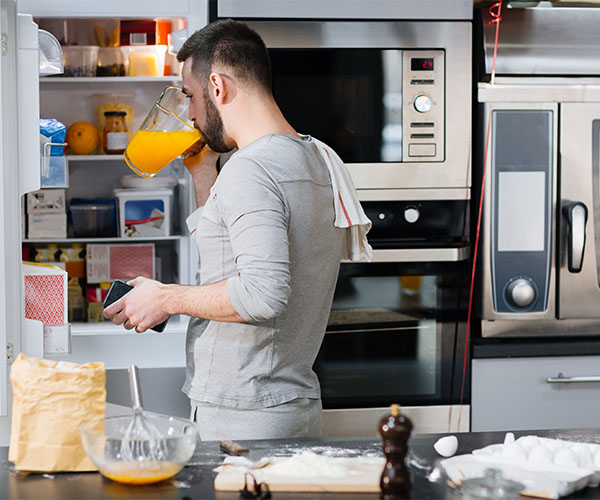
Conclusion
Navigating the complexities of an ice machine running but not making ice can be a challenging yet rewarding journey. Throughout this guide, we’ve equipped you with the essential knowledge and steps needed to tackle this issue confidently. As we conclude, let’s recap the key points and reinforce the importance of regular maintenance to avoid future disruptions:
- Quick Diagnosis: Always start with the basic checks—ensure your machine is properly powered and that the water supply is adequate.
- Troubleshooting Common Issues: We’ve covered how to identify and fix common problems like frozen lines, clogged filters, sensor failures, and other mechanical malfunctions.
- Proactive Maintenance: Regularly cleaning and maintaining your machine not only extends its lifespan but also ensures it runs efficiently.
To maintain optimal performance of your ice machine, consider these final tips:
- Monitor and Adjust: Regularly check and adjust the settings on your ice machine to suit environmental changes, especially during extreme seasons.
- Seek Professional Help When Needed: Don’t hesitate to call a professional if the issue seems beyond basic fixes, especially to handle complex mechanical faults.
We encourage you to share this post with others who might find it beneficial and invite you to comment below with your experiences or additional tips. Together, we can ensure that a minor hiccup with your ice machine doesn’t turn into a major headache.
FAQs on Ice Machine Issues: Running but Not Making Ice
- Why is my ice machine running but not producing ice?
- This could be due to several issues, including low water flow to the machine, clogged filters, or frozen water lines. Ensure the water supply is active and check for any visible blockages or frost.
- How can I troubleshoot a frozen water line in my ice machine?
- To resolve a frozen line, first turn off the ice machine and unplug it. Thaw the line using a hair dryer set on low, or wrap the lines with warm cloths. Avoid using direct high heat as it can damage the lines.
- What should I do if the filters are clogged?
- Replace the water filters if they haven’t been changed according to the manufacturer’s recommendations, typically every 6 months. A clogged filter can restrict water flow, preventing ice production.
- How do I reset my ice machine?
- Most ice machines have a reset button or procedure detailed in the user manual. Generally, you can turn the machine off, unplug it for a few minutes, and then plug it back in to reset the system.
- When should I call a professional to fix my ice machine?
- If basic troubleshooting does not resolve the issue, or if you suspect a mechanical failure such as a malfunctioning pump or motor, it’s best to call a certified technician to prevent further damage.
- Can regular maintenance prevent my ice machine from running without making ice?
- Yes, regular maintenance such as cleaning the machine, changing filters, and checking for mechanical wear can prevent most common issues. Schedule periodic inspections and cleanings as recommended by your manufacturer.
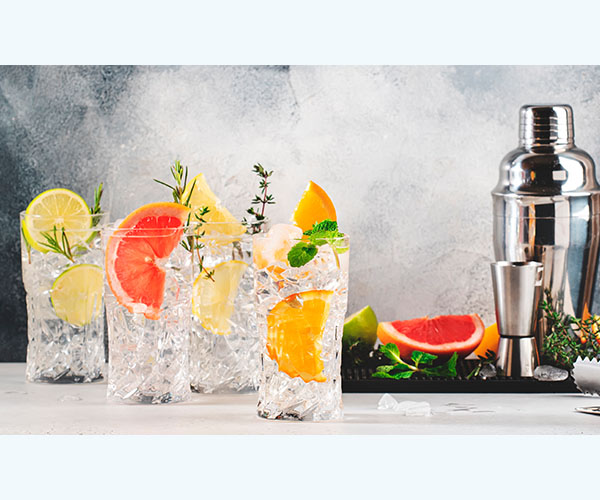