Introduction
A countertop ice maker is a convenient appliance for those who love a steady supply of ice for drinks, parties, or even road trips. However, when your countertop ice maker isn’t making ice, it can quickly turn from a helpful gadget to a source of frustration. Understanding how these machines work and knowing how to troubleshoot common issues can save you time and money. This guide is designed to help you diagnose and fix problems with your portable ice maker. Whether you’re dealing with no ice production, strange noises, or simply want to ensure your machine runs smoothly, this comprehensive guide has you covered. https://amzn.to/3WoePQf
Understanding How Countertop Ice Makers Work
To effectively troubleshoot why your countertop ice maker isn’t making ice, it’s essential to understand the basics of how these machines operate. Unlike traditional refrigerators with built-in ice makers, portable ice makers are self-contained units that require manual water filling. Here’s a breakdown of the main components and their functions:
1. Water Reservoir: The water reservoir is where you manually pour water to be converted into ice. This is typically located at the bottom of the unit, and the capacity can vary depending on the model. It’s crucial to use clean, preferably filtered water, to avoid mineral buildup and ensure the purity of the ice.
2. Water Pump: Once the machine is powered on, the water pump draws water from the reservoir into the ice-making mechanism. The efficiency and functionality of this pump are vital for the machine to operate correctly. A malfunctioning pump can lead to no water reaching the ice-making components, resulting in no ice production.
3. Ice Tray and Mold: The ice tray is where the ice is formed. Depending on the design, this can be a metal or plastic tray with molds in various shapes. The machine cools these molds to a freezing temperature, allowing water to solidify into ice cubes. The design of the tray and molds can affect the size and shape of the ice cubes produced.
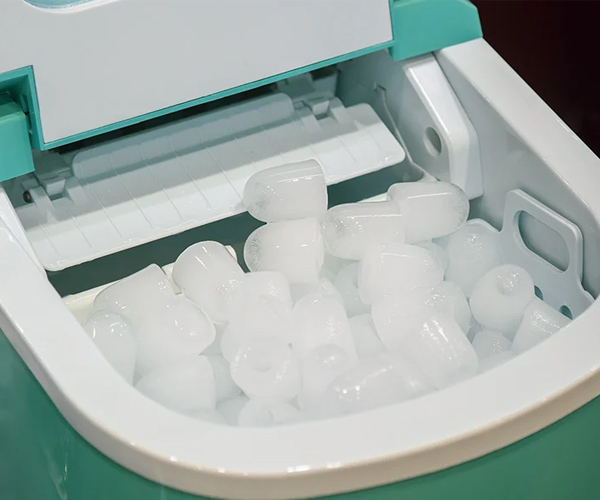
4. Cooling System: The cooling system is perhaps the most critical component. It includes a compressor, condenser, and evaporator, similar to those found in refrigerators. The compressor circulates refrigerant through these components, absorbing heat from the water to lower its temperature and freeze it into ice. If any part of this system fails, the machine won’t be able to produce ice.
5. Sensors and Control Panel: Modern countertop ice makers come equipped with sensors that monitor water levels and ice production. These sensors can detect when the water reservoir is low or when the ice tray is full, automatically stopping the ice-making process to prevent overflow or damage. The control panel allows users to select ice cube sizes, start or stop the machine, and sometimes even set timers.
Understanding these components helps in identifying where a problem might originate when your countertop ice maker isn’t working. Whether it’s a simple issue like low water levels or a more complex one like a malfunctioning compressor, knowing the basics can make troubleshooting more straightforward.
Common Issues That Prevent Ice Production
When your countertop ice maker isn’t making ice, it can be due to a variety of reasons. Here, we break down some of the most common issues and provide detailed insights into why they occur and how they can be fixed.
1. No Power: One of the most straightforward issues to diagnose is a lack of power. This can happen if the machine is not properly plugged into an electrical outlet, or if there’s an issue with the outlet itself. Before assuming there’s a more serious problem, always check that the power cord is securely connected and that the outlet is functioning. You can test the outlet with another appliance to ensure it’s working correctly. Additionally, some models have a power switch on the back or side; make sure it’s in the “on” position.
2. Water Supply Problems: Water supply issues are another common culprit. If the water reservoir is empty or the water pump is malfunctioning, the machine won’t have the necessary water to create ice. Start by checking the water reservoir. If it’s empty, fill it up and see if the machine begins the ice-making process. It’s also possible that the water pump might be clogged or broken. In such cases, you may hear a buzzing sound, which indicates the pump is trying to work but can’t move the water. Cleaning the pump or replacing it might be necessary.
3. Ice Tray Malfunctions: The ice tray or mold is where the water freezes into ice. If the tray is misaligned or obstructed, it can prevent the machine from making ice. This issue might occur due to an accidental bump or a mechanical malfunction. Carefully inspect the ice tray for any visible signs of damage or obstruction. In some cases, ice cubes can get stuck in the tray, causing a jam. Gently remove any stuck ice and realign the tray if needed.
4. Cooling System Failures: The cooling system is critical for the ice-making process. It consists of the compressor, condenser, and evaporator. If any of these components fail, the machine won’t be able to cool the water and freeze it into ice. Common signs of cooling system issues include the machine running constantly without producing ice or the exterior of the machine becoming excessively warm. In such cases, it might be necessary to consult a professional for repair, as dealing with refrigerants and cooling systems can be hazardous.
5. Sensor Issues: Many modern ice makers use sensors to monitor various functions, such as water levels and ice production. If these sensors malfunction, they can give false readings, causing the machine to stop working. For instance, a faulty water level sensor might incorrectly indicate that the reservoir is empty, preventing the machine from starting. Similarly, a broken ice level sensor might stop the machine even when the ice tray isn’t full. Sensor issues can often be resolved by resetting the machine or replacing the faulty sensors.
Understanding these common issues provides a solid foundation for troubleshooting when your countertop ice maker isn’t making ice. The next section will guide you through a detailed troubleshooting process, helping you identify and resolve specific problems.
Step-by-Step Troubleshooting Guide
When your countertop ice maker isn’t working, it can be daunting to figure out where the problem lies. However, with a systematic approach, you can often identify and fix the issue yourself. This step-by-step troubleshooting guide will walk you through the process, from basic checks to more detailed inspections.
1. Preliminary Checks: Before diving into more complex troubleshooting, start with the basics. Ensure that the ice maker is properly plugged into a working electrical outlet. If the machine isn’t receiving power, it won’t be able to operate. Check the power cord for any signs of damage, such as fraying or cuts, which could be causing a short circuit. Additionally, make sure the power switch on the machine is turned on.
Next, inspect the water reservoir. An empty reservoir is a common reason for a countertop ice maker not making ice. Fill the reservoir with clean water, ensuring it reaches the minimum fill line. If your machine has a water level indicator, use it to check if the water level is sufficient. Sometimes, even a small amount of water below the required level can prevent the machine from starting.
2. Checking for Error Codes: Many modern countertop ice makers are equipped with digital displays that show error codes when something goes wrong. These codes can provide valuable clues about the issue. Refer to your user manual to decode these messages. Common error codes might indicate problems like a low water level, a full ice tray, or issues with the cooling system. If you’re unsure about the meaning of an error code, consult the manufacturer’s website or contact customer support. https://amzn.to/3WoePQf
3. Inspecting the Water Supply: If the water reservoir is full but the machine still isn’t making ice, the issue might lie with the water supply system. Start by checking the water pump. A malfunctioning pump can prevent water from reaching the ice tray. Listen for a buzzing sound, which can indicate that the pump is working but struggling. If the pump is clogged, you can try cleaning it by flushing it with warm water. In some cases, the pump might need to be replaced.
Also, check the water inlet valve and tubing for blockages. Over time, mineral deposits or debris can clog these components, restricting water flow. Cleaning these parts can often resolve the issue. If you’re using hard water, consider using filtered water to prevent future clogs.
4. Examining the Ice Tray Mechanism: The ice tray is where water is frozen into ice cubes. If the tray is misaligned or blocked, the machine can’t properly form ice. Carefully remove the ice tray and inspect it for any stuck ice or debris. Sometimes, a simple realignment is all that’s needed. Make sure the tray is securely in place and that there are no obstructions in the path of the tray’s movement.
Additionally, check the ice tray motor. This motor moves the tray into position for water to be poured in and then back to release the ice cubes. If the motor isn’t working correctly, the tray won’t move as needed. Listen for any unusual noises that could indicate a problem with the motor. If necessary, consult your user manual for instructions on how to replace a faulty motor.
5. Assessing the Cooling System: The cooling system is essential for freezing water into ice. It consists of a compressor, condenser, and evaporator. If your ice maker isn’t producing ice, the cooling system might be the culprit. Start by listening to the compressor. A healthy compressor should make a steady humming noise. If you hear clicking or no noise at all, the compressor might be malfunctioning.
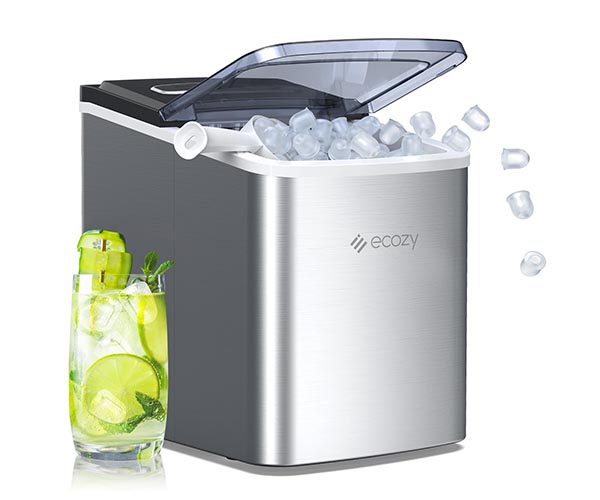
Next, check the condenser coils. These coils can accumulate dust and debris, reducing their efficiency. Clean the coils with a vacuum or a coil brush to ensure proper heat dissipation. Also, inspect the evaporator for frost buildup. If the evaporator is covered in frost, it could indicate a refrigerant leak or a faulty defrost system. These issues usually require professional repair.
6. Testing the Sensors and Electronics: Sensors play a crucial role in the operation of your countertop ice maker. They monitor water levels, ice levels, and temperature. If these sensors malfunction, they can prevent the machine from operating correctly. Start by checking the water level sensor. This sensor detects the amount of water in the reservoir. If it’s dirty or faulty, it might give a false reading, preventing the machine from starting. Clean the sensor with a soft cloth and check if the issue is resolved.
The ice level sensor is another critical component. It detects when the ice tray is full and stops the ice-making process to prevent overflow. If the sensor isn’t working, the machine might stop making ice even when the tray isn’t full. You can test the sensor by manually triggering it and observing the machine’s response. If the sensor isn’t functioning correctly, consider replacing it.
In some cases, the control board or electronic components might be the issue. This is a more complex problem and often requires professional diagnosis and repair. If you’ve exhausted all other troubleshooting steps and the machine still isn’t working, it’s time to call in a professional.
In this first part of our comprehensive guide, we’ve covered the basics of how countertop ice makers work, common issues that can prevent ice production, and a detailed troubleshooting guide. Remember, when dealing with electrical appliances, safety should always be your top priority. If you’re unsure about any of the steps or if the problem seems too complex, don’t hesitate to seek professional help.
Stay tuned for the next part, where we’ll dive into maintenance tips to prevent future issues, discuss when it’s time to seek professional help, and answer frequently asked questions about countertop ice makers.
Maintenance Tips to Prevent Future Issues
Preventive maintenance is key to ensuring your countertop ice maker operates efficiently and lasts for years. Regular upkeep not only helps in avoiding sudden breakdowns but also ensures the quality of the ice produced. Here are some essential maintenance tips:
1. Regular Cleaning and Descaling:
Over time, mineral deposits from water can build up inside the machine, affecting its performance. This is especially true if you’re using hard water. Descaling the ice maker every few months is crucial to prevent this buildup. Here’s a simple cleaning routine:
- Turn Off and Unplug the Machine: Always disconnect the ice maker from the power source before cleaning to avoid electrical hazards.
- Remove and Wash Removable Parts: Take out the ice tray, water reservoir, and any other removable components. Wash them with warm, soapy water and rinse thoroughly.
- Use a Descaling Solution: Fill the water reservoir with a mixture of water and descaling solution or vinegar. Run a cleaning cycle according to the manufacturer’s instructions. This helps dissolve mineral deposits.
- Rinse Thoroughly: After descaling, run a couple of cycles with clean water to remove any residual cleaning solution or vinegar taste.
- Wipe Down the Exterior: Use a damp cloth to wipe the exterior surfaces of the machine, removing dust and grime.
2. Proper Water Filtration:
Using filtered water in your countertop ice maker can significantly extend its life. Unfiltered water can introduce minerals and impurities into the machine, leading to scale buildup and affecting the taste of the ice. Consider installing a water filter in the machine, if it has a provision for one, or use pre-filtered water. This not only protects the machine’s components but also ensures you get clear, pure ice cubes.
3. Seasonal Maintenance Checklist:
If you use your ice maker seasonally, such as only during summer, it’s essential to perform a thorough maintenance routine before storing it away and when taking it out of storage:
- Before Storage: Clean and dry all components thoroughly. Leave the machine in a well-ventilated area for a few hours to ensure all moisture has evaporated. Store it in a cool, dry place to prevent mold and mildew growth.
- After Storage: Clean the machine before use, even if it was cleaned before storage. This removes any dust or potential mold that may have formed. Check all parts for damage or wear and replace if necessary.
4. Checking for Wear and Tear:
Regularly inspect the machine for signs of wear and tear, especially moving parts like the ice tray and water pump. Look for cracks, loose components, or any signs of corrosion. Early detection of these issues can prevent more significant problems down the line.
5. Maintaining the Cooling System:
The cooling system is vital for the machine’s operation. Ensure that the condenser coils are clean and free from dust. This can be done with a vacuum or a soft brush. Keeping the cooling system in top shape ensures efficient ice production and prolongs the machine’s lifespan.
When to Seek Professional Help
Despite thorough troubleshooting and maintenance, there may be instances where your countertop ice maker isn’t making ice due to more complex issues. In such cases, professional repair services might be necessary. Here’s how to determine when it’s time to call a professional:
1. Persistent Electrical Issues:
If your ice maker repeatedly trips the circuit breaker or shows signs of electrical malfunctions, such as flickering lights or erratic operation, it’s best to consult a professional. Electrical problems can be dangerous and should be handled by qualified technicians.
2. Cooling System Failures:
The cooling system, including the compressor and refrigerant, requires specialized knowledge to diagnose and repair. If you suspect a refrigerant leak or the compressor isn’t functioning correctly, professional service is recommended. Handling refrigerants requires proper equipment and expertise due to environmental regulations and safety concerns.
3. Unusual Noises:
While some noise is normal in any appliance, unusual sounds like grinding, banging, or squealing can indicate serious internal issues. These noises often suggest problems with the motor, fan, or other mechanical parts. A professional can accurately diagnose and fix the problem, preventing further damage.
4. Malfunctioning Sensors and Control Boards:
If you’ve tried resetting the machine and checking sensors with no success, the issue might lie with the control board or sensors. These components are complex and may require professional diagnostics to pinpoint the problem accurately.
5. Warranty Considerations:
If your ice maker is still under warranty, it’s advisable to contact the manufacturer or an authorized service center for repairs. Attempting to fix the machine yourself may void the warranty. Always check the warranty terms before proceeding with any repairs. https://amzn.to/3WoePQf
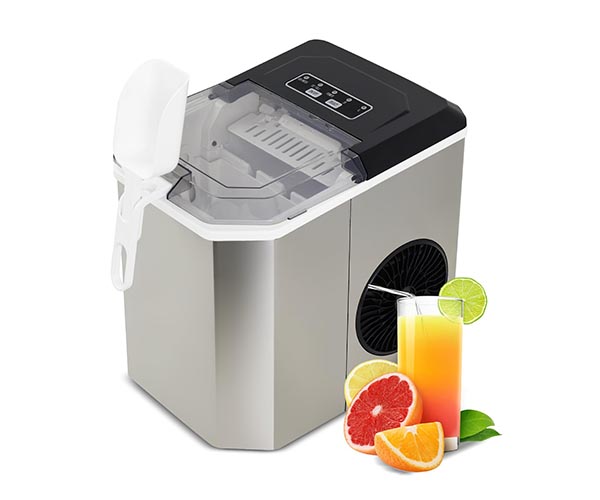
Frequently Asked Questions (FAQs)
1. What should I do if my countertop ice maker is making strange noises?
Strange noises can be alarming, but they often have simple explanations. If your ice maker is making unusual sounds, check if the ice tray or other components are properly aligned and not obstructed. If the noise persists, it could indicate a mechanical issue, such as a faulty motor or fan. In such cases, it’s best to consult a professional to avoid further damage.
2. How often should I clean my countertop ice maker?
For optimal performance and hygiene, clean your ice maker every three months or more frequently if you use it daily. Regular cleaning prevents mold and bacteria buildup and ensures the ice produced is safe and clean. If you use hard water, more frequent descaling may be necessary to prevent mineral buildup.
3. Can I use distilled water in my ice maker?
Yes, using distilled water in your countertop ice maker is recommended, especially in areas with hard water. Distilled water is free of minerals and impurities, which helps prevent scale buildup and extends the life of your machine. Additionally, it produces clearer, better-tasting ice.
4. What are the signs that my ice maker needs to be replaced?
Over time, even with regular maintenance, an ice maker may reach the end of its lifespan. Signs that it might be time for a replacement include frequent breakdowns, decreased ice production, strange odors or tastes in the ice, and increased noise levels. If repair costs are nearing the price of a new machine, it may be more economical to replace the unit.
5. How can I improve the efficiency of my countertop ice maker?
To ensure efficient operation, keep the machine in a cool, well-ventilated area. Avoid placing it near heat sources or in direct sunlight. Use clean, filtered water to reduce mineral deposits and clean the machine regularly. Additionally, make sure the machine is level and stable to prevent any operational issues.
Conclusion
A countertop ice maker is a valuable addition to any kitchen or bar, offering the convenience of fresh ice on demand. However, like any appliance, it requires regular maintenance and occasional troubleshooting to keep it running smoothly. By understanding the common issues and how to address them, you can extend the life of your ice maker and enjoy hassle-free ice production.
Remember, while many problems can be resolved with basic troubleshooting, don’t hesitate to seek professional help for more complex issues. Proper care and timely repairs can make all the difference in the longevity and performance of your machine.
Whether you’re an ice enthusiast or just need an ice maker for occasional use, following these guidelines will ensure you always have a reliable supply of ice. Thank you for reading, and feel free to share your experiences or tips in the comments below. For more helpful guides and tips, subscribe to our blog and stay updated!