Introduction
Have you ever pondered the reason behind your ice maker’s ability to function silently without releasing even a single cube? You are not the only one. This widespread issue not only causes disruptions to your daily need for fresh ice, but it also indicates that there may be inefficiencies in the operation of your equipment, which may eventually lead to more expensive problems or complications. This issue should be addressed as soon as possible in order to save time, minimize the amount of energy that is consumed, and extend the life of your ice machine. Within this all-encompassing guide, we will delve into the workings of ice machines, identify the most common problems that they face, and present solutions that are step-by-step in order to restore your machine to its optimal level of function. https://amzn.to/3WoePQf
Understanding Your Ice Machine
In order to properly diagnose the problem with your countertop ice maker, it is essential to have a fundamental understanding of the mechanics that govern how your ice machine functions. The fact that these machines are so small and convenient does not change the fact that they are susceptible to a number of problems that hinder them from successful ice production. We will now take a more in-depth look at how they function and the typical issues that arise:
- Basic Operation: At its core, an ice machine freezes water from a water reservoir, uses a compressor to cool the refrigerant, and a thermostat to monitor the temperature. The process begins when water fills the ice mold and the refrigeration cycle chills it until ice is formed. Once the ice reaches the desired temperature, the machine triggers a heat cycle to loosen the ice, which is then ejected into the bin.
- Common Components:
- Compressor: The heart of the ice machine, responsible for circulating the refrigerant that cools the water into ice.
- Evaporator: Where the water freezes into ice before being harvested.
- Condenser: Releases heat removed from the interior to the outside environment.
- Thermostat: Monitors the temperature and controls the start and stop cycles of the ice making process.
- Water Pump: Ensures the water circulates over the evaporator, enhancing the efficiency of the ice-making process.
- Typical Issues:
- Clogged Water Filter: Can restrict water flow, leading to insufficient water in the ice mold.
- Faulty Thermostat: If the thermostat fails, it may not trigger the necessary refrigeration cycle to freeze the ice or the heat cycle to release the ice.
- Refrigerant Leak: Low refrigerant levels can result in poor cooling performance, meaning the water never reaches freezing temperatures.
- Electrical Issues: Problems with the machine’s electrical system can prevent the compressor, pump, or motor from operating correctly.
By gaining an understanding of these components and the roles they play within your ice machine, you will be able to determine the reason why your countertop ice maker is unable to produce ice. Your ice maker will continue to run properly and efficiently if you perform routine maintenance and troubleshooting on these important areas at the appropriate times. This will avoid the majority of problems from becoming more severe.
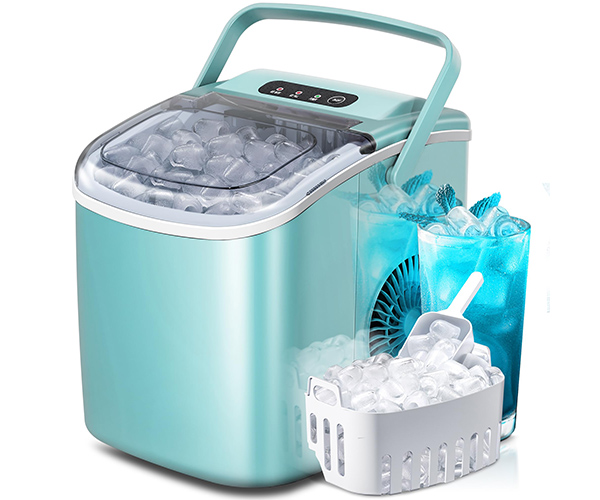
Common Reasons Why Ice Machines Fail to Produce Ice
Ice machines, particularly countertop ice makers not freezing, can be frustratingly finicky. Understanding why your ice maker isn’t working properly is the first step towards a solution. Here are some of the most common issues that might prevent your ice machine from producing ice:
- Frozen Water Lines
- Symptoms: No water flows into the ice mold, and the machine sounds like it’s trying to operate without results.
- Diagnosis: Check for visible frost on the lines or lack of water flow when the cycle begins.
- Solution: Thaw the water lines using a hair dryer or by unplugging the machine and letting it warm up in a room-temperature environment.
- Faulty Water Pump
- Symptoms: The machine makes noise, but no water is being pumped into the ice tray.
- Diagnosis: Listen for a humming sound from the pump; check for water movement in the reservoir.
- Solution: Replace the water pump if it fails to circulate water despite being powered.
- Clogged Filter
- Symptoms: Slow water flow, smaller or incomplete ice cubes.
- Diagnosis: Inspect the water filter for debris or sediment build-up.
- Solution: Clean or replace the filter to ensure unrestricted water flow.
- Thermostat Issues
- Symptoms: Ice machine doesn’t get cold enough, or ice production is intermittent.
- Diagnosis: Use a thermometer to check the internal temperature.
- Solution: Adjust or replace the thermostat to ensure accurate temperature control.
- Low Refrigerant Levels
- Symptoms: Ice machine runs but doesn’t get cold, leading to a countertop ice maker not freezing.
- Diagnosis: This issue generally requires a professional, as refrigerant levels must be checked with specialized tools.
- Solution: Refill the refrigerant, typically handled by a certified technician to comply with regulations.
Not only do these common problems bring to light the complex nature of the operations of ice machines, but they also show the significance of performing routine maintenance and identifying problems as efficiently as possible. You will be able to rapidly diagnose and fix the majority of the issues that hinder your ice machine from producing ice in an efficient manner if you have a thorough awareness of these aspects.
Preventative Maintenance Tips
It is essential to do routine maintenance on your countertop ice maker in order to guarantee that it will continue to function well and to prevent frequent problems such as the countertop ice maker not freezing. In addition to extending the lifespan of your machine, doing routine maintenance helps to guarantee that the ice it generates is of a high quality. In order to keep your ice maker in the best possible condition, here are some important maintenance tips: https://amzn.to/3WoePQf
- Regular Cleaning: Ensure that your ice maker is cleaned regularly to prevent mineral build-up that can affect the machine’s efficiency and the taste of the ice. Use a simple solution of water and vinegar for effective cleaning.
- Inspect and Replace Filters: To keep your ice maker running smoothly, check and replace the water filters according to the manufacturer’s guidelines. This is crucial as it affects the water quality and overall performance of the machine.
- Routine Checks for Water Flow: Make sure that there is a consistent water flow to the ice maker. Irregular water flow can lead to ice slabs that are not properly formed, contributing to the issue of your countertop ice maker not freezing properly.
- Keep the Surroundings Cool: The area around your ice maker should be kept cool and well-ventilated. Excessive heat can cause the internal temperature to rise, which hampers the freezing process.
- Check the Freezer Temperature: Regularly check that the freezer temperature is set correctly as per the ice maker’s specifications. Incorrect temperature settings can be a primary reason for ice makers not freezing.
- Regularly Inspect the Condenser Coils: Dirty or clogged condenser coils can lead to inefficient machine operation. Cleaning the coils can prevent problems related to overheating and poor freezing.
- Seal Checks: Ensure that the door seals are intact. Air leaks can cause frost buildup which can impact the efficiency of the ice making process.
- Professional Inspection: If you notice persistent issues, it might be worth getting a professional to inspect your machine. They can offer more detailed maintenance and identify issues that aren’t easily noticeable.
By according to these preventative maintenance guidelines, you will be able to improve the performance of your ice maker and extend its lifespan, so ensuring that it will regularly generate ice of a high quality. In addition, routine maintenance assists in the early diagnosis of problems, such as a countertop ice machine that does not freeze, which leads to the prevention of costly repairs in the future.
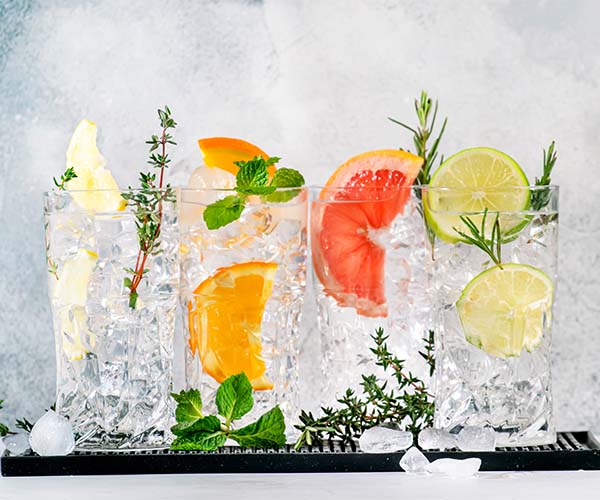
ice machine running but not making ice
When your ice machine is running but not making ice, it’s crucial to delve deeper into more sophisticated troubleshooting methods. Understanding these advanced techniques can be the key to solving more complex issues that aren’t resolved by basic checks. Here are some strategies to consider:
- Inspect Electrical Connections:
- Ensure that all electrical connections are secure. Loose wiring can interfere with the operation of the ice machine.
- Check for any signs of wear or damage on the wires and connectors. Replace any faulty components.
- Sensor Checks:
- Ice machines rely on various sensors to function correctly. These include thermostats, water level sensors, and ice-full sensors.
- Test each sensor’s functionality with a multimeter. Refer to your ice machine’s service manual for specific diagnostic procedures.
- Examine the Condenser Coil:
- The condenser coil is essential for the heat exchange process. A dirty or blocked coil can hinder the ice machine’s ability to freeze water.
- Clean the condenser coil thoroughly, removing all dust and debris. Ensure proper airflow around the coil.
- Check the Evaporator Plate:
- Ice forms on the evaporator plate; issues here can prevent ice production.
- Inspect the plate for scale build-up or signs of damage. Clean the plate with a nickel-safe cleaner if necessary.
- Water Flow Analysis:
- Inadequate water flow can prevent the ice tray from filling, thus stopping ice production.
- Verify that the water inlet valve is fully operational. Check for clogs or leaks and ensure that it is receiving the correct water pressure.
- Control Board Diagnostics:
- The control board is the brain of your ice machine. A malfunction here can lead to various issues.
- If equipped, use the self-diagnostic function to check for error codes. Consult the manufacturer’s guide to interpret these codes.
- Refrigerant Level and Pressure Check:
- Incorrect refrigerant levels can severely affect the ice-making process.
- This check should be done by a certified technician, as it involves handling potentially hazardous materials and specialized equipment.
Each of these steps requires careful attention to detail and safety precautions. Always disconnect power to the unit before attempting any repairs and consider consulting with a professional if the issue persists or the repairs are beyond your comfort level. Troubleshooting your ice machine when it is running but not making ice can be intricate, but with the right tools and a bit of know-how, you can diagnose and potentially fix the issue, restoring your machine’s functionality and efficiency.
Case Studies: Real-Life Troubleshooting of Ice Machines
Delving into real-world scenarios, these case studies illustrate common issues and effective solutions for when your ice machine is running but not making ice. Here are detailed accounts from various settings:
- Restaurant Scenario:
- Problem: A high-volume restaurant noticed their ice machine was running constantly but failed to produce ice.
- Diagnosis: Technicians found a severely clogged water filter and low refrigerant levels.
- Solution: Replacing the water filter and refilling the refrigerant resolved the issue.
- Lesson: Regular maintenance is crucial, especially in high-demand environments.
- Office Breakroom Ice Maker:
- Problem: Employees reported that the ice maker was humming but not producing ice.
- Diagnosis: A quick inspection revealed a frozen water line.
- Solution: Thawing the water line and installing a water line heater prevented future occurrences.
- Lesson: Preventative measures can avoid common cold environment issues.
- Home Ice Machine Troubles:
- Problem: A family’s undercounter ice machine stopped making ice right before a large gathering.
- Diagnosis: Faulty thermostat reading temperatures incorrectly.
- Solution: After recalibrating the thermostat, the machine resumed normal ice production.
- Lesson: Sometimes, a simple recalibration can restore function without replacing parts.
- Event Venue’s Ice Production Delay:
- Problem: An event venue’s ice machine was running but only producing minimal ice during peak hours.
- Diagnosis: Insufficient water flow due to an old, inefficient pump.
- Solution: Replacing the water pump increased ice production to meet demands.
- Lesson: Upgrading equipment components can enhance performance under high-load conditions.
Each of these cases underscores the importance of understanding the specific mechanics and potential problem areas of ice machines. From restaurants to home use, ensuring your machine is not just running but also producing ice efficiently can save both frustration and expense. Regular checks and proactive maintenance are the best strategies to keep your ice machine in optimal condition.
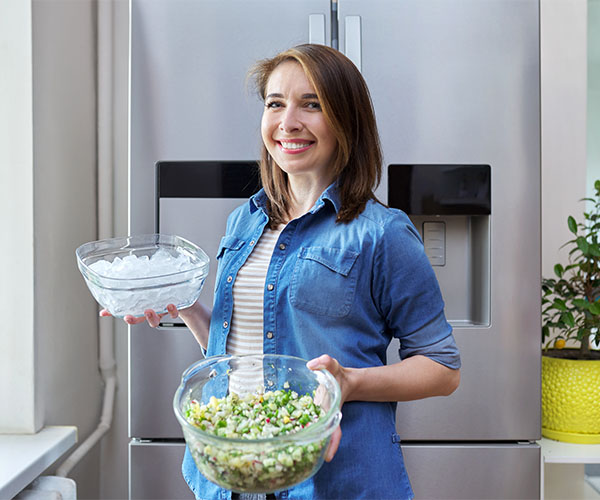
Conclusion
Throughout this guide, we’ve tackled the frustrating issue of an ice machine running but not making ice. Now that you understand the common causes and the steps to diagnose and fix them, you’re well-equipped to handle these disruptions effectively. Here’s a brief recap of key points to remember:
- Regularly inspect your machine for signs of frozen water lines and ensure timely maintenance to prevent blockages.
- Stay vigilant for symptoms indicating a faulty water pump, and don’t hesitate to replace it if needed.
- Keep an eye on your machine’s filter; a clogged filter can be a silent culprit in many efficiency issues.
- Always monitor thermostat settings and recalibrate if discrepancies arise.
- Be aware of the refrigerant levels, as low levels are often a subtle yet common reason for malfunction.
By implementing these tips, you not only enhance the functionality of your ice machine but also contribute to its longevity and operational efficiency. As you apply this newfound knowledge, remember that maintenance is continuous, and catching issues early is key to preventing the ice machine running but not making ice scenario.
- Invite to share experiences: We’d love to hear how these solutions worked for you. Comment below with your experiences or additional tips!
- Professional help: If troubleshooting seems overwhelming, don’t hesitate to contact a professional.
By staying informed and proactive, you ensure that your ice machine remains a reliable resource in your daily life.
FAQs About Ice Machine Issues
- Why is my ice machine running but not producing ice?
- This often occurs due to a water supply issue. Check if the water valve is fully open and the supply line isn’t kinked or frozen. If water flow isn’t the problem, inspect the freeze sensor and ensure it’s functioning properly.
- What should I do if the water line to my ice machine is frozen?
- Thaw the water line using a hair dryer on a low setting or by wrapping the pipes in warm towels. Avoid using direct high heat as it can damage the lines. Once thawed, check for leaks that could have caused water to freeze.
- How can I tell if the water pump in my ice machine is faulty?
- Signs of a faulty water pump include strange noises during operation or water failing to flow into the ice mold. Inspecting the pump for blockages or mechanical failure is advised; replacement may be necessary if the pump is not working.
- What maintenance can prevent my ice machine from failing?
- Regular maintenance should include:
- Cleaning and replacing filters annually.
- Checking and cleaning the condenser coils every six months.
- Ensuring the thermostat is calibrated correctly to avoid over or under freezing.
- Regular maintenance should include:
- Can low refrigerant levels cause my ice machine to stop making ice?
- Yes, low refrigerant levels can prevent the machine from producing ice. If the machine runs but doesn’t get cold, a refrigerant top-up or leak repair might be required. Note that handling refrigerant typically requires a professional.
- Why is it important to regularly clean my ice machine?
- Regular cleaning prevents the build-up of lime scale and mold, which can block water flow and degrade ice quality. It also helps maintain efficient operation and prolongs the lifespan of the machine.
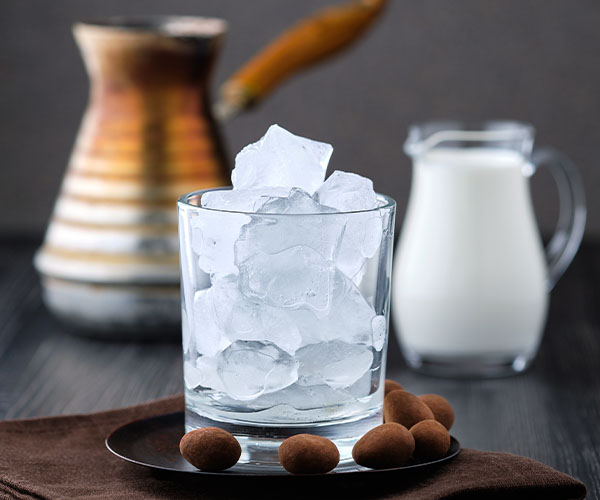